Winning the Printing Race: Screen-Printing Maintenance
October 25, 2019
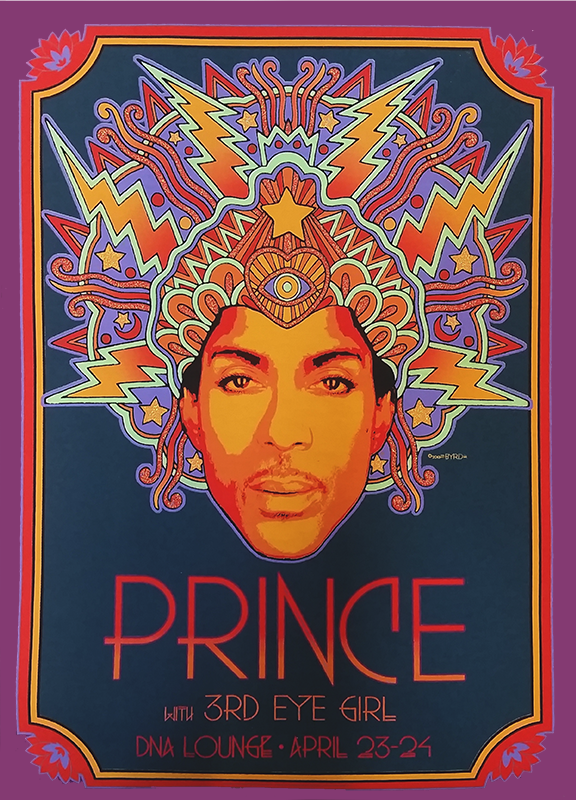
In an article published by Impressions Magazine, Kieth Stevens gives us valuable tips about the importance of screen printing maintenance.
When a race car driver wins a race and stands at the podium to accept the coveted prize and recognition, he gets the praise, accolades and the headlines. But how many people’s shoulders do you think he is standing on – a few a dozen? Hundreds?
There is the team that sets up the suspension; the team that built the engine; the team who chose the tire durometer…The fuel mixture? How about the team who built the transmission etc. The point is that once the driver sits in the driver’s seat, there have been thousands of hours and decisions that have been made in order for the driver to even have a chance to win.
At a recent seminar about special effects printing, I spoke about how each tool used in screen printing has its purpose and why its upkeep and maintenance is important to the end result: A great print!
I used a race car analogy to illustrate my points:
It costs a lot to design and build a race car, and each component used in the car has a purpose, whether it’s a lug nut to secure the tire or a seat belt buckle to hold the harness in place – once you are setting up a design on the screen press, many decisions have already been made and the printer’s experience in printing the design can make the print a winner or a looser depending on all the pre-press preparations.
Are the screen tensions up to snuff (tight)? Are the squeegees sharp and the durometers correct? Is the emulsion thickness enough? Is the film opaque enough? These are just some of the pre-press preparations that need to be made. Why is it so important to get the pre-press prep done right?
Let’s say that some of the pre-press decisions weren’t working out on the press, what do you do? If you need just a little extra ink deposit on one color for example, can you re-burn a screen if the mesh opening isn’t large enough? Not ideal, but it’s possible – if time and money isn’t an option. However, if you have a selection of squeegee durometers on hand to choose from, you may be able to save yourself some time and select a lower durometer squeegee (softer) and get away without having to re-burn the screen with a lower mesh count.
In another scenario, when printing a white design on dark fabric, did you consider adding an extra coat of emulsion on the white under-base screen? That could really help with the opacity of your white inks.
Here’s why the little details in pre-press matter: If you had a press in your garage that printed dollar bills, would you let it run out of paper – or ink? Would you have critical spare parts ready if needed? Well if you are a screen printer, you are the machine in the garage that prints dollar bills. I’ve been in that position, and I had to make sure I did everything I could beforehand to guarantee that my machine was printing as many "dollar bills" and for as long as I could.
Just as in a race, you can’t win the race if you can’t start or finish. So starting the print run as soon as you can with the proper preparation assures that you will stand in the winner’s circle at the end!
Related Articles: Pointers for Pre-Press Success Part 1 / Pointers for Pre-Press Success Part 2
Kieth Stevens is the Western regional sales manager for International Coatings. He has been screen printing for over 42 years and teaching screen printing for more than 12 years, is a regular contributor to International Coatings’ blogs and won SGIA’s 2014 Golden Image Award.