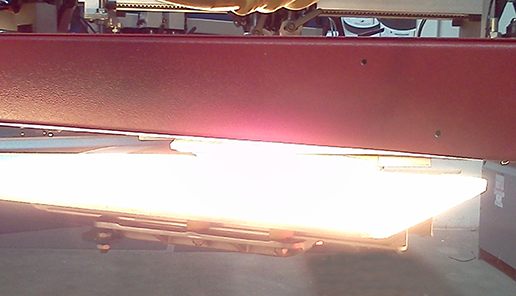
Here is a recent tip from Mark Brouillard that was published in
Printwear:
Flashing ink is a standard practice in the industry, especially when printing a white underbase on a dark substrate. However, many printers are unaware that they actually can over-flash their inks. So what, you may ask? Isn’t the purpose of the flash to cure the ink so that other colors can be printed on top?
The purpose of the flash is to get the ink to a “gel” state so that the next coat of ink printed on top of it does not pick up the flashed color. It may also be used to help minimize the amount of wet ink accumulating at the back of the next screen. Most inks achieve a gelatinous state when the ink reaches 180 degrees F to 200 degrees F, depending on the ink. The ink film should just feel dry to the touch, not completely cured. Test the flash by slowly working up to the proper temperature.
As production progresses, keep an eye on the temperature as the platens heat up and the flash temperature or distance to the substrate may need to be adjusted. When the ink is over-flashed, it can cause inter-coat adhesion problems with the subsequent ink layers, meaning the other inks printed on top may not adhere fully to the over-flashed ink layer. The inks may become very tacky, peel off the over-flashed ink, or even partially wash off.