In a recent article published by Printwear Magazine, Kieth Stevens gives us expert insight into ink buildup during printing.
I've come across a lot of discussions lately regarding buildup. What is buildup, and what causes it?
I have visited many shops in my career, and one of the first things I look for are ink shavings below a press. Ink shavings are the telltale sign there is a buildup issue on the backs of screens.
WHAT IS BUILDUP?
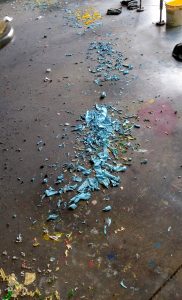
It’s when the ink from a previous deposit of ink leaves a residue on the back of the next screen. Having ink residue is not a problem in itself; it’s when the residue continues to add up and builds up into a paste that, over time, will begin to cause a problem. The buildup causes issues such as screen clogging and image distortions for subsequent screens.
Some shops get used to it, cope with it, and think that it’s just part of the business, but when I look at their shop floor, I can tell that there
is a problem. Cleaning off the buildup from screens takes time and effort and if the buildup is extensive, or starts after only a short print run, the loss in production time and efficiency can affect a shop's bottom line substantially.
I’m not saying buildup is avoidable in every situation or with every ink, but it can be controlled or minimized to a degree.
SO, WHAT'S THE CAUSE?
There are three factors that can contribute to ink building up:
HEAT OR OVER FLASHING
Plastisol is a thermo-plastic and fuses with heat. Everyone wants inks that flash quickly, and as a representative for an ink manufacturer, I can attest that fast-flashing is always a topic when we test new ink products. However, creating an ink that has a low fusing point (i.e., gels fast under the flash) is a two-edged sword. If the ink fuses too quickly, then the residual heat from flashes and heated platens can begin to gel the printed ink during the printing process.
In some cases, the heat can transfer to the inks that are still in the screen. Once the ink has gotten to a fusing or gel point, it can’t go back to its original fluid state and will begin to coagulate, thus sticking to the backs of the next screens. Ink manufacturers try and keep a tight balance of low curing or fusing but not too low.
PIGMENT TYPE
Another cause is the amount or type of pigments used. White inks are heavily pigmented, and when printing a light sky blue, for instance, the color will contain mostly white pigment. You may see the ink begin to build up. Similarly, fluorescent-colored inks also have a greater tendency to build up due to the pigments.
GARMENT COLOR
One other issue stems from the type or color of the garment. Many of the large printers recognize the fact that white shirts contain starches that react to the liquids in the inks and begin to thicken below the screens. If the paste left by the buildup is examined and looked at carefully, one will see that it contains a lot of fibers mixed with something resembling a binder. When printing on a white or clear underbase, you may notice that the same design and inks do not have the same buildup issue.
HOW CAN IT BE REDUCED?
Most printers try to reduce the buildup on a particular design by adding a flash to the problem color that is building up. This quick fix will certainly work; however, if the heat from that extra flash is not monitored closely, the additional heat may very well add to the problem. Over long production runs, as the platens heat up, it’s usually necessary to adjust and reduce the flash times. As I said before, too much residual heat can also create a buildup issue. Newer high-end flash units and print machines have sensors that can automatically compensate and reduce overheating.
Adding a curable reducer to ink that builds up is another way of minimizing the buildup issue. Some machine manufacturers offer optional equipment which sprays a mixture of cold water and silicone mist after the flashing step to quickly cool the print and platen down and control excessive heat transfer.
Although buildup can’t always be avoided, it can be controlled by monitoring excess heat throughout the entire print process. I cannot stress enough how vital the residual/excess heat control is to mitigating buildup issues. Ultimately, less buildup translates to less time spent in the cleanup, which equals to a smoother print run and more to the bottom line.