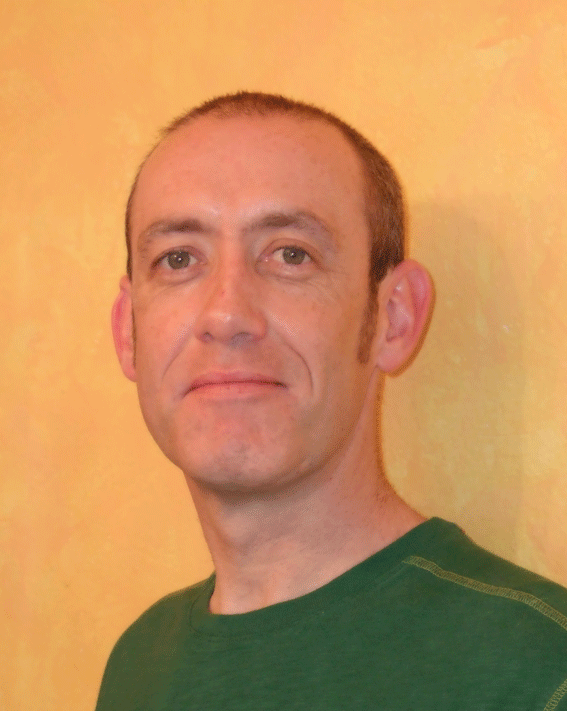
Many of our customers who call in for technical help are routed to our Print Applications Manager, Ed Branigan. Ed helps troubleshoot the problem with the customer, which can sometimes be tricky when the troubleshooting is done over the phone or via e-mail. Ed often receives calls regarding “ink problems,” so here are some tips on what to look out for when you encounter printing issues:
“When a customer calls to talk about issues with curing, the conversation often starts with a statement. It usually runs something like “the ink came right off of the shirts
after I cured them.”
My response is always to ask how the person is sure that the ink was cured. Some get indignant, some not, but the general response to my query is usually to be told that they know because they ran the printed garments through the dryer. Some might also mention that the dryer settings were the same as they always were and the problem had never arisen before so therefore the ink must be bad.
Sometimes the ink indeed might be bad. Once in a while, an error in the manufacturing process can occur. We hope that it’s not that often but if it does, we are equipped to figure out what the problem is, where it occurred and how to quickly fix it. Most professional ink manufacturers have such quality control procedures in place.
The point that I’m getting at here is: There’s only one way to know for sure that the ink on the shirt is cured and that’s to wash it. If the ink stays on the shirt and doesn’t crack or fade, then it’s cured. (Also see our previous blog entries on
curing and
dryers). If your production order is worth say, $15,000, wouldn’t it pay to print a sample, cure it, then wash test it before running production? This is true when working with expensive materials or even running a large amount of cheap materials, but it is especially true when working with fabrics that bleed. It pays to test
every time, then test again.
Bleeding, or dye migration, can occur immediately, the next day, a week or even a month after printing. Printing a sample, curing it, then waiting at least 24 hours should be standard operating procedure for any shop printing on fabrics that may be prone to bleeding issues (poly blends or 100% polyesters).
Imagine printing 1000 garments, shipping them, then a week later receiving a call from your customer wondering why the ink was changing color. It happens.
With curing, it’s a different set of issues but just as important. Not all dryers are the same and not all of them behave the same way every day.
General dryer maintenance issues aside, plastisol inks have two critical needs that must be met in order for the ink to cure or fuse: One is temperature and the other is the amount of time that the ink spends under that temperature. Dryers need to be checked regularly to make sure that they are indeed hitting the required temps and printers need to follow the manufacturer’s recommendations for curing times.
Once this is done, it is still crucial to test. Different types of fabrics can absorb or reflect heat and this can sometimes alter the temperature in the dryer chamber especially if it’s running all day or night. Certain types of inks are sensitive to atmospheric changes in temperature and humidity, which can affect curing.
The only way to be absolutely sure that the ink that you are about to print will stay on all of the garments, is to print one and wash test it first. Even then you can only be certain about that particular ink on that particular fabric.
Save yourself time, money and a lot of headaches by
always testing before production.”
For more information, check out our previous blogs:
Curing Ink Correctly?
Which Dryer Should I Buy?
Problems Curing White Ink?
Why So Many Whites?
Also check out this page about
bleeding and dye migration from our
Facebook page.
For more on International Coatings’ products, visit our website at
www.iccink.com.