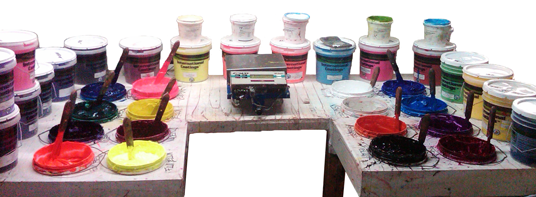
This article by Kieth Stevens was recently published in
Impressions Magazine:
As the implementation of the Consumer Product Safety Improvement Act of 2008 (CPSIA) permanently prohibited certain phthalates from being used in children’s products, the screen printing industry has since scrambled to meet the demands of the new regulations. Even though the legislation does not specifically address apparel, it does specify children’s products, and many large retailers have mandated that all their apparel products for children be phthalate compliant.
(Editor’s Note: Children’s products are broken down into two categories: 12 and under for lead (100 ppm) and 3 and under for lead and the six permanently prohibited phthalates.)
As such, this affects, to a large degree, the ink used for screen printing, since plastisol ink can contain prohibited phthalates. However, in order to pass the testing mandated by the Consumer Product Safety Commission (CPSC), the entire screen printed design on a garment must be phthalate-compliant. In the past two years, I have heard and experienced a few nightmarish situations regarding phthalate-compliant (PC) ink kitchen conversions, or haphazard conversions where cross-contamination still occurred.
Why is a clean conversion so important? If your clients insist on phthalate-compliant garments and your finished product does not pass the final test, it can become a very costly problem. Following are some points to consider when converting your ink kitchens to become phthalate-compliant:
1. To determine whether you are completely phthalate-compliant, you need to take several careful steps. First, use a reputable ink supplier that is committed to providing safe and compliant ink. When purchasing ink at your local screen printing supply store, ensure that the ink you are getting states that it is phthalate-compliant (some will also state that it is “Non-Phthalate” or “Phthalate-Free”), as the supplier may have non-compliant ink stocked.
2. After you have secured a clean ink supply, your ink kitchen needs to be thoroughly cleaned and disinfected. Think of the phthalates as germs or bacteria, in that they can’t be seen, so you don’t know where they could be hiding. The allowable amount of prohibited phthalates is ridiculously low and is measured aggregately, so it does not take much to fail the test. Shelves, counters, floors — everything that can touch the garment — need to be cleaned.
The best way to further establish that there is no cross contamination is to actually discard all your non-compliant inks (in accordance with local, state and federal regulations), because if you are using even one product in your factory (e.g. an ink that has a unique property) that is not phthalate-compliant, then you are playing with fire.
Discarding all non-compliant products is a drastic, but necessary, step to take to avoid any accidental cross contamination issues. If you are not ready to part with all of your inks, you could store them at a separate location to avoid contaminating the phthalate-compliant inks when printing for a customer who mandates compliant product.
However, beware that should you use the non-compliant product on the same printing machines and equipment you are using for printing with compliant product(s), the machines and equipment also will be contaminated and you will have to clean and disinfect it again.
3. I don’t profess to have a lot of knowledge regarding cleaning solutions or emulsion chemistry, but I advise that you ensure your supplier is aware that you require that all the products contacting your ink is compliant. To my earlier point about discarding all non-compliant inks, if you use just that one ink that is non-compliant, your cleaning solution system (if you have a recirculating tank system, for example) and your cleaning sink may get contaminated, thus cross-contaminating all of your other equipment.
I recently helped convert a large printing facility where it had cross-contamination issues in the past, and the amount of ink we ended up discarding amounted to more than seven pallets. I am happy to report that this company now is completely clean and running full speed ahead.
4. Utensils often are overlooked in the process of decontaminating ink kitchens. Make sure the stir sticks, spatulas and mixing buckets or containers are cleaned with a compliant cleaning solution. Be especially vigilant if the utensils have been used to mix non-compliant inks before, in which case you need to be sure all the corners, nooks and crannies have been scrubbed with a stiff brush.
5. Lastly, clean your squeegees. Take apart your automatic squeegees and use a stiff brush to remove all old ink that is left in the crevices and cracks. Be sure to inspect the blades for any residual non-compliant ink as well.
All these steps may seem over the top, but I have seen how much business can be lost — not to mention how tarnished a reputation can become — if your product does not pass the phthalate compliance test just because your ink kitchen and handling process was haphazard and allowed for cross contamination. To avoid any dire consequences, do it right the first time.
BIO:
Kieth Stevens is the Western regional sales manager for International Coatings. He has been teaching screen printing for more than 10 years and is a regular contributor to International Coatings' blogs. For more information, visit iccink.com and read the company’s blog at internationalcoatingsblog.com.
International Coatings manufactures a complete line of phthalate-compliant
screen printing inks, including a wide variety of
whites,
specialty inks,
special effects inks,
color matching systems,
additives and reducers. For more information on our products, please visit our website at
www.iccink.com.
International Coatings: The Intelligent Choice