The Right Tools For The Job - Part 3
November 17, 2015
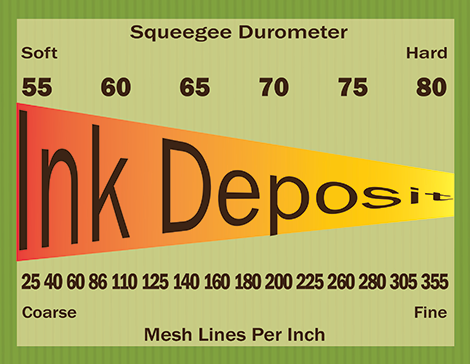
Here is the third part of Kieth's article about the importance of using the right tool for the job and knowing what the tool can do. If you missed the previous blogs, here you can read Part 1 and Part 2. You can also read the full article (PDF) from here.
MESH
Just as squeegee hardness affects ink deposit, so does mesh count: The lower the mesh count, the larger the ink deposit. But are there any other features differentiating one mesh type over another?
Thread Count
As most printers know, mesh controls the flow of ink once the squeegee passes over the image. The general rule of thumb is that the lower the mesh count is per inch (or cm), the larger the amount of ink flow.
However, there are some instances where it is possible to go higher in the amount of threads per inch/cm and get an even larger amount of flow. How so? Let’s discuss the next aspect about mesh: Thread diameter.
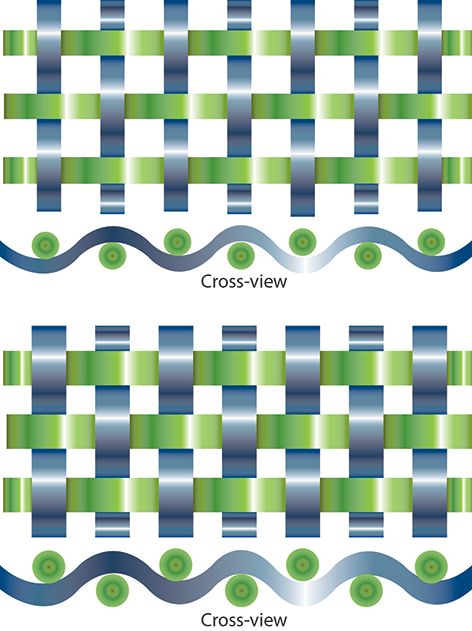
Thread Diameter
Believe it or not, not all meshes at the same thread count function the same. This has to do with the actual thread diameter used to create the mesh. Obviously, the thicker the thread diameter, the higher the tension you can achieve when stretching the screen. The thicker thread is also less likely to cause the screen mesh to pop or break.
Breaking mesh is bad, right? Agreed – however, there are some options to consider. Some mesh is made with thinner thread diameter (same mesh count) and if used with care, won’t have to be stretched to such a high level as the thicker thread.
What is the advantage of using the thinner thread diameter? For the same mesh count, the thinner thread diameter allows for a greater percentage amount of open area within the mesh, thus resulting in higher image definition and increased ink flow.
So if the thread diameter is smaller, going to a higher mesh count is possible to still achieve a larger amount of ink flow and finer detail definition in the print.
Here is a simple guide that will help in choosing the right mesh counts for the right job:
Mesh Count: 25, 40 – Usage: Coarse Glitter Inks
Mesh Count: 60, 86 – Usage: Specialty inks, such as puff or high-density, fine shimmers, glitters or metallics
Mesh Count: 110, 155 – Usage: Use where a large deposit of ink is needed, such as athletic numbers, printing white on black fabric, low-detail art or heavy white ink
Mesh Count: 160, 180, 200 – Usage: Good for printing underbase white to create a softer overall feel, good medium-sized mesh count for medium-detailed artwork. The 200-count mesh can be a happy medium screen selection for when a 230 mesh is too fine and a 155 mesh is too coarse.
Mesh Count: 230, 280, 305 – Usage: Low ink deposit, works well for halftone printing, simulated process or CMYK process printing
Mesh Count: 355 – Usage: Very low ink deposit, generally used by very experienced printers only. Often used for printing 65 line or higher halftones for very detailed images
PUTTING IT ALL TOGETHER
So with all this said it is hard to explain the total relationship that occurs when the squeegee touches the ink and applies the ink to the shirt.
A soft squeegee pushing low viscosity ink (thin) through a coarse screen can apply too much ink. But use that soft squeegee to push a thick ink through a fine mesh and it can spell disaster.
Similarly, when a hard squeegee is used to push a thin ink using an open mesh or if the same hard squeegee is used to push thin ink with a lot of pressure through a fine mesh, both scenarios may result in less desirable printing outcomes.
Knowing how one tool or another can affect the outcome of the print, I am able to use the knowledge and adjust the variables to make a bad ink look better or a good ink look outstanding. I liken printing to an art form, where a good printer can use his tools to create the best possible print. Much of the finesse in screen printing will only come with experience, but knowing the basics about the relationship of how different tools can affect different aspects of the print outcome is half the battle.
Kieth Stevens is the Western regional sales manager for International Coatings. He has been teaching screen printing for more than 10 years and is a regular contributor to International Coatings’ blogs.
Blade samples courtesy of Fimor, Serilor brand. Print samples courtesy of Fimor.
International Coatings manufactures a complete line of non-phthalate screen printing inks, including a wide variety of whites, specialty inks, special effects inks, color matching systems, additives and reducers. For more information on our products, please visit our website at www.iccink.com