The Right Tools For The Job - Part 1
November 04, 2015
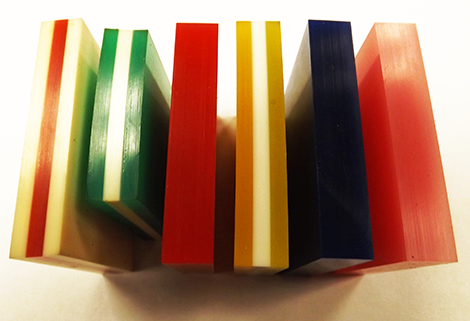
This article by Kieth Stevens was recently published in Specialist Printing Worldwide Magazine, Issue One:2015. We'll publish the article in two parts, or you can read the full copy that is posted on our website here.
My father is a Master carpenter and I learned early on that in order to do the best job possible, you not only need to have the skills and training, you also need to have the proper tools.
Over the years, I realized the truth of what he was saying, especially when I was Off-Road racing in the late ‘90s and had to rebuild my race car every 3 months to meet the deadline for the next competition. In order to be as efficient as possible I had to have the right tools at the ready so that I not only got the job done quickly but also wouldn’t damage the parts I was working on.
I now reference this simple revelation every time I conduct a screen print seminar: In order to do the best job possible in silk-screen printing and – more importantly - be profitable, we need to understand the tools that we have at our disposal.
Screen printers have many tools in their arsenal; however, most don’t understand the relationship between how one affects another, or how prints can easily be improved using simple adjustments and, most importantly, how this relationship can affect your profitability.
There are many variables and facets that can make a print go from average to great, or for production speeds to go from sluggish to fast. Take for example two of the most common, yet important “tools” in our arsenal: Squeegees and mesh. Each of these affects how ink gets printed or “laid down” onto the substrate. Let’s first talk about squeegees, one of the most misunderstood and under-utilized tools, in my opinion:
SQUEEGEES
Squeegees are one of the must-have basic tools for a screen printer and come in many hardness levels (durometer). Typically, squeegees start at a soft 55 durometer to a hard 80 durometer. To complicate matters, there are sandwich-type squeegee blades on the market that stack a soft and a hard blade or sandwich a hard blade between two soft blades. In addition, some blade edges are rounded, while others are square, and yet others are pointed.
With all the various choices available, it’s easy for a screen printer to get confused as to which type to use for what. Here is the basic rule: A soft squeegee lays down more ink than a hard squeegee.
Durometer/Hardness
Now let me explain a bit more about this:
- 50-60 durometer blades are considered “soft” and will deposit more ink. Choose this durometer for heavily-textured fabrics such as fleece or sweatshirts, to lay down more ink (may help with fibrillation) or for use with special effects inks, such as gels and puffs.
- A 60-75 durometer designation ranks “medium” on the hardness scale. This hardness range is good for general printing.
- The hardest option is an 80 durometer blade. It will deposit less ink and is great for printing fine detail or four-color process prints
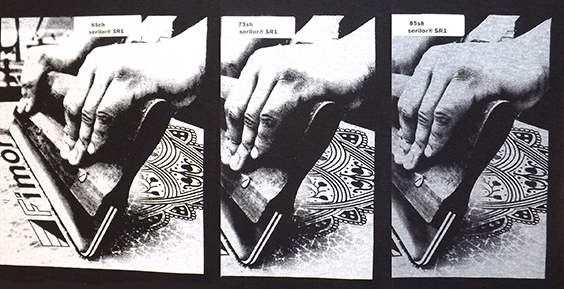
Part 2 will follow next week, where Kieth will discuss composite blades, squeegee profile, and handles. Don't miss it!
Kieth Stevens is the Western regional sales manager for International Coatings. He has been teaching screen printing for more than 10 years and is a regular contributor to International Coatings’ blogs.
Blade samples courtesy of Fimor, Serilor brand. Print samples courtesy of Fimor.
International Coatings manufactures a complete line of non-phthalate screen printing inks, including a wide variety of whites, specialty inks, special effects inks, color matching systems, additives and reducers. For more information on our products, please visit our website at www.iccink.com