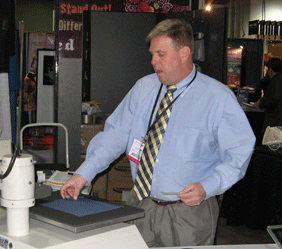
Why is testing so important? As we are seeing more and more diverse types of fabric and materials coming from all parts of the world, the need to do proper testing is becoming a MUST in screen printing. Here is our Northeast Regional Sales Manager, John Levocz with more insight on this topic:
“Gone are the days of just printing on 100% cotton and some 50/50 garments. Printers are now being asked to print on a variety of materials ranging from 100% poly, spandex, nylon and performance wear. These materials are being imported from all over the world and no two seem to be the same. Some of the poly fabrics bleed very quickly while some resist bleed very well. Some nylons have a coating while others do not.
This being said, it is very important in this day and age to develop testing parameters for the materials you need to print. It is also a good time to check and see what new inks and additives are on the market to help you print on these materials successfully.
Polyester dyes seem to start bleeding (dye migration) when they hit temperatures above 300 degrees Fahrenheit (149° C). To control the bleeding issue, try test printing with a low cure product or adding a
low cure additive into inks to be printed on 100% polyester. Do a print test and let it sit for a few days as sometimes it can take time for the bleed to show itself. Starting with a good bleed-resistant white (such as International Coatings’
711,
714 White or
7041 Paramount White) is always the best starting point.
To check and see if the nylon you are getting ready to print on might have a coating that will hinder adhesion, pour a small amount of water on the nylon. Go about your business for ten minutes and then check the nylon. If the water has beaded up like mercury on the material and is not soaking in, you could have a possible adhesion problem. Try wiping an area with isopropyl alcohol and repeat the water test. If the water soaks in after wiping the material, you know what you need to do to get the ink to adhere.
The other parameter we need to achieve on many of these materials is stretch. First determine how much stretch is needed. Is the print a left chest or possibly a full front print? They will both require a different amount of stretch. For a small left chest print, a plastisol ink might have enough stretch built in to achieve acceptable results. For a full front or back print you might need to add a
stretch additive to give the ink more stretch so it does not crack. (For more on
printing on stretch fabrics, visit our previous blog entry).
If possible, try and get some material from your suppliers so you can do testing before the job needs to go out. Spend the time doing the testing and recording the results and you will be on your way to being able to handle the difficult materials we are being asked to print on in today’s market.”
For more on International Coatings’ products, please visit our website at
www.iccink.com.