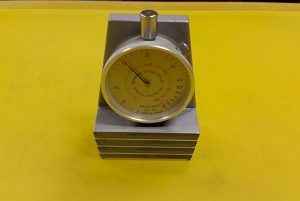
Screen-mesh tension plays a very important factor in your final print. Although many factors can affect your print, screen tension should not be overlooked, as it will impact things such as emulsion coating, registration and ink deposit.
Before printing, screens must be coated and burned (exposed). If a screen is lacking proper tension, exposure will become more difficult than it should be. A loose screen that has been coated with emulsion runs the risk of not burning properly, having cracked emulsion or an excessive number of pinholes that show up in the print. These are problems that will occur before printing even begins.
If a design requires more than one screen, tension still will be an issue. A loose screen is more prone to movement while doing a run of prints and can mess up the registration. This slows down the printing process and the output will largely be useless if the design is misaligned.
If, while printing, a screen sticks to the garment, this also is a result of lack of proper tension. Screens with little or no tension don’t bounce off the garment as they should. The screen sticks to the garment, resulting in an excessive ink deposit. A heavy amount of ink on a shirt means a rough-finish feel, rather than a print that is light and smooth to the touch.
A simple way to check screen tension is by using a tension meter. This device measures the tension of stretched mesh in units of Newtons. Proper tension typically measures between 25 and 35 N/cm2. Any value in that range ensures a properly tensioned screen, which will produce a good final print.
Since screens face wear and tear with long production runs and washing with pressurized hoses, it is important to check them occasionally to ensure they have the proper tension needed for the job.
Abigail Franco is a screen printer from Los Angeles. She received a screen printer certification from Pasadena City College and in 2017 was the recipient of the Tom Frecska Student Printing Competition award. She currently is an intern at International Coatings.