Sustainable Printing Practices: Part 2
August 21, 2020
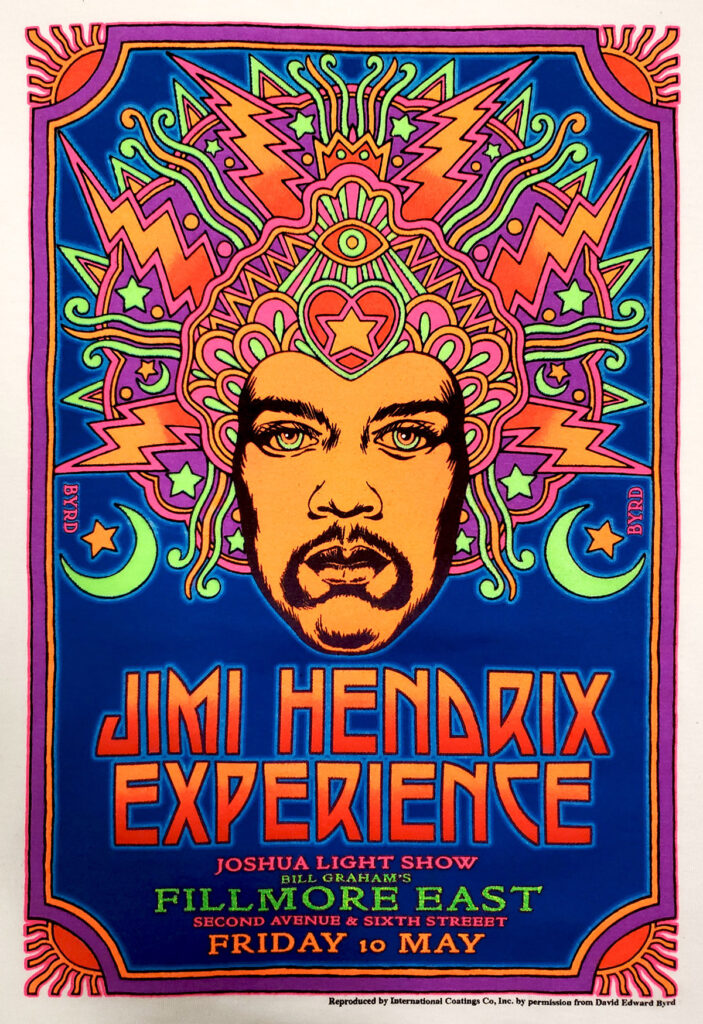
Earlier this year, we published the first part of this article, Sustainable Printing Practices: Part I. Here is the second part of this article, which was published in Impressions Magazine.
The second article in this two-part series addresses everything from dark and synthetic substrates to test printing.
In Part I, we covered sustainable practices in screen prep, choosing among the multitude of inks, screen-printing production and more. The takeaway: Many screen-printing processes may not be considered green or sustainable, but they certainly can be altered to be as sustainable as possible.
In the second installment of this two-part series on sustainable screen-printing practices, let’s discuss considerations that must be made when printing on dark substrates and polyester, ink costs, flashing, curing and test printing.
Dark Substrates and Polyester
Most plastisol or acrysol inks use a standard white underbase for printing on dark substrates. For water-based inks, many screen printers prefer to use a discharge ink, which basically bleaches the cotton shirt during the curing process, creating the equivalent of a “white” underbase. Subsequent top colors will appear more vibrant.
Discharge inks often contain toxic chemicals, sometimes even the carcinogen formaldehyde. Beware that chemicals in the ink may be released into the air and may be toxic to the operator. The environmental and human impact associated with using discharge inks and the additional energy-output requirements for pre-heating pallets or extra flash units should be considered in your analysis.
When printing on polyester substrates, consider the fabric content and how it was dyed. Most medium-to-dark garments can bleed or sublimate residual dye during the curing process due to the heat needed to cure water-based, plastisol and acrysol inks. To contain the bleeding dye, you may need to print a gray or black dye-blocking ink to help absorb the excess dye. This means other inks must be added to the printing process; thus, extra heat and dryer duration will be needed to achieve a proper cure.
You also can print on polyester or polyethylene/non-woven fabrics using low-cure inks. Does your ink line accommodate low-temperature curing — typically around 275°F? Not all shirts are 100% cotton, and many of today’s trendy eco-friendly or recycled-material shirts are synthetic blends, requiring bleed-blocking ink technology or low-cure capability.
Another Ink Consideration
Can your ink be printed through high mesh counts? This may be an important factor if your shop offers halftone, photorealistic or detailed prints. Be sure to check for this characteristic in your ink.
Ink Coats
Since the acrylic resins in acrysols cost about three to four times more per pound than regular plastisol (PVC) resins, finished inks end up costing about double per pound. The resin makes up about only 35% of the total ink.
However, the new acrysols still contain almost no solvents; they are considered to be 100% solid. What you apply on to the shirt remains there, so you get what you pay for. Nothing evaporates or is wasted.
When using high-solids, water-based inks, expect about 35%-45% of the product to be solvents or other liquids that will be released during the curing process. If using regular water-based inks, the solvent content usually is 60%-70%, so keep that in mind when comparing finished-ink costs and yields.
Flashing
With regular plastisol inks, the need to flash colors can be avoided, when possible. Normally, you only need to flash white underbases or during the process of printing a few colors (an average of one to three flashes for an 11-color design on a dark substrate, for example).
Plastisol inks are fused with heat, typically around 320°F, and can gel at even lower temperatures. Heat is your friend when you want to cure the ink, but it can become an enemy if not controlled.
With many — but not all — of the new high-solids, water-based inks, it is necessary to flash each color due to ink build-up underneath the screens. Frequent flashing often results in either a reduction in the number of colors you can print or the need to buy larger screen-printing machines with more heads and more open spaces to accommodate additional flashes and cooldown stations between colors. I often have seen five screens and four flashes being used to print a single-color, white logo. The results look great, but the process consumes unnecessary time and energy.
I never thought that such an involved print process was an option years ago when I was printing shirts daily. If I had told my supervisor that we should try using five screens, double-stroked, for a one-color logo, I would have been the butt of many jokes. Now, however, many large, vertical brand-name manufacturers are doing it. Hopefully, they can recoup the costs in other areas since they provide the garment and full packaging for the brands.
Curing
Standard plasistol and acrysol inks cure at about 320°F in 60 seconds. However, many now can cure at about 275°F in the same amount of time.
Remember, the thicker the ink deposit, the longer it will take to cure. When printing on dark polyester fabric using a dye-blocking gray ink with a white underbase printed and possibly other top colors, slightly more time in the dryer may be required to fully cure the thicker ink deposit.
Water-based inks cure at about 320°F but may require an additional 30-60 seconds under the heat to evaporate all the solvents. Inks that take twice as long in the dryer or require higher temperatures to cure use more energy and are not as sustainable as ones that require less time and lower temperatures.
Test Printing
Disposing garments that are not printed correctly the first time is wasteful. Paying employees twice for the same work also cuts into profits. Let’s face it: Doing things correctly the first time is more profitable and sustainable than doing things twice.
I’m a big proponent of test printing when a new fabric, technique or ink is involved. Give yourself a couple of days to test before starting production and perform a wash test about 24 hours after printing. Many inks require several hours for an optimal cure. Similarly, wait at least overnight or 24 hours before performing a scratch test.
If you are printing on dark polyester/synthetic fabrics, extend the time for test printing. Dye migration often doesn’t happen immediately after printing, and may even take several days or a week to occur. Imagine sending a completed order only to have the shirts returned several weeks later due to dye-migration issues.
Here’s an example: I often like to cook for friends and family; when doing so, I don’t plan on cooking food twice. I make decisions very carefully so as not to be wasteful and so that my guests aren’t left waiting. I certainly don’t buy double the food in the event that I have to repeat the cooking process. Not only would this be costly, but it would be wasteful and unsustainable.
Research your options when deciding on which products or processes are more sustainable, but also consider them in a larger context. Just because a product may sound environmentally friendly doesn’t mean it’s true, especially when you consider the overall processes, energy consumption, ingredients and more.
Kieth Stevens is the Western regional sales manager for International Coatings. He has been screen printing for more than 42 years and teaching screen printing for more than 12 years, is a regular contributor to International Coatings’ blogs and won SGIA’s 2014 Golden Image Award. He can be reached at kstevens@iccink.com.