Sustainable Printing Practices: Part 1
June 23, 2020
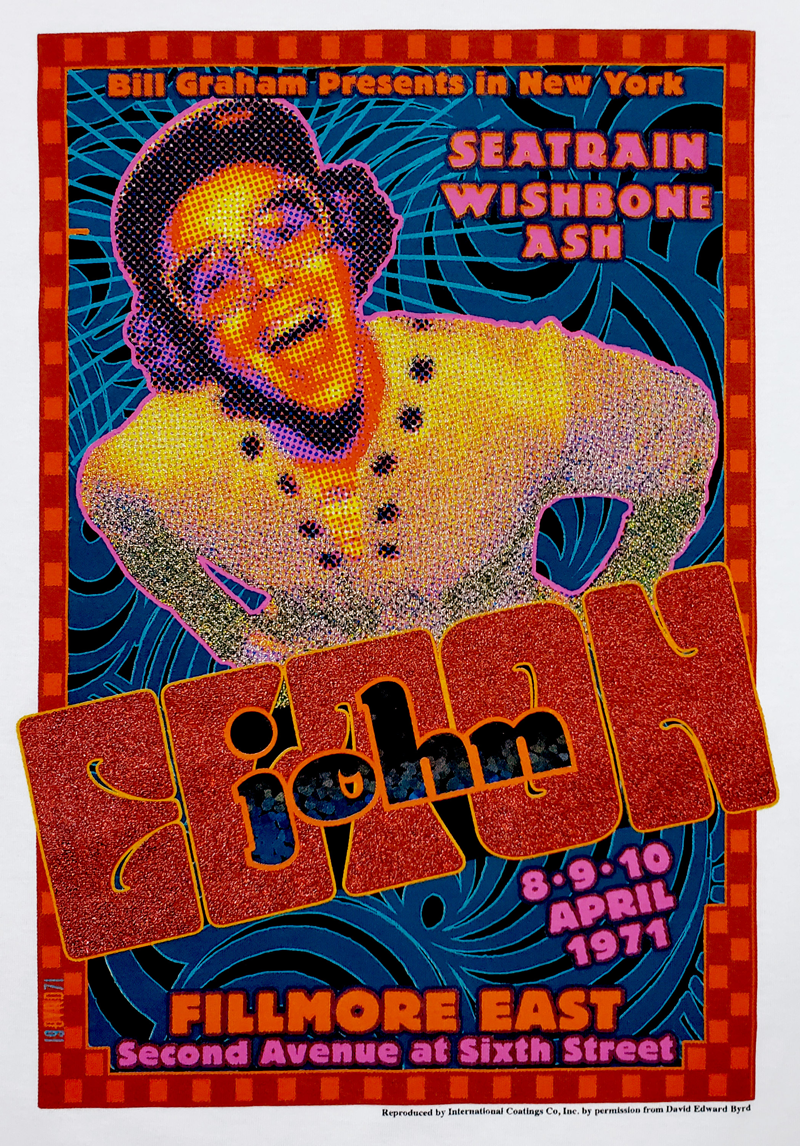
This article by Kieth Stevens recently appeared in Impressions Magazine.
The first installment in this two-part series focuses on eco-friendly factors in everything from screens to inks.
I’m in the process of adding a bathroom and kitchen to a building on my property. During the process, decisions need to be made, including the types of doors, windows, counter tops and cabinets to be installed. Do I use tile for the shower or a pre-fabricated enclosure? What colors should I paint the walls?
These decisions are important for achieving the desired look and feel, but installation must be done correctly the first time. I may change my mind on a color or something minor, but any major structural change would involve more costs and result in waste.
Screen printing is similar; many of its processes may not be considered green or sustainable, but they certainly can be altered to be as sustainable as possible. Any screen printer can implement methods to streamline the processes while also being more sustainable.
Screen-Prep Emulsion
Making screens correctly the first time not only will save money, but also have the least effect on the environment. Once you’ve decided on the screen mesh for a particular design, ensure it is tight enough. Loose, sloppy screen mesh will distort your prints and result in wasted time and effort in correct registration.
Remember to properly dehaze and degrease your screen mesh using environmentally friendly products. When drying the mesh, avoid using a fan, which can blow dirt and dust on the screen and cause pinholes in your emulsion stencil.
Ensure the emulsion coating is clean and free of dust or contaminants. This also applies to the exposure glass and film. Use an exposure calculator for accuracy; also, ask your emulsion supplier’s representative for help to ensure the best possible screen preparation.
Burning and Developing Screens
This process uses more precious water and chemicals, so it’s important to get it right the first time. Check your exposure times with a calculator weekly or at least once a month. Store your screens in a light-safe environment. Light is like lead poisoning for screens; it will slowly expose screens and fine halftone dots will start to disappear.
Today, the most common film is the inkjet type; it’s convenient but there is some plastic film that can be recycled, but seldom is. With the computer-to-screen (CTS) trend, a plastic film backing no longer exists, which certainly reduces plastic use. However, if a screen needs to be burned again, then doubled ink costs must be considered.
The newest trend, the CTS laser, uses no consumables and achieves extremely high resolutions. It comes with a high initial cost, but is much more environmentally friendly in the long term. It’s better to burn the screen correctly the first time; however, if you have to burn it again, there are no consumables washed down the sink during development.
Ink Choices
How sustainable are your ink choices? The following are pros and cons of each main ink type available in today’s marketplace.
Plastisol: The most common screen-printing ink, today’s plastisols don’t contain the restricted phthalates that were banned several years ago, nor do they include hazardous lead or other dangerous chemicals that were prevalent about 40 years ago.
Most screen printers have used plastisol ink and are accustomed to its characteristics and curing parameters. This ink type contains 100% solids, meaning there is no gassing off and minimal loss when it is printed and cured. It contains minimal to trace amounts of solvents; doesn’t dry in the screen; and is very opaque and easy to manage
Acrysol: This is a newer, PVC- and phthalate-free ink type. Most work like plastisol, but some fall short of being a substitute because of the newness factor. During the past couple of years, much has improved with regard to printability and hand. Some even print and feel as well or better than traditional plastisol.
Water-Based and High-Solids Water-Based: Many tout water-based ink as the most eco-friendly or sustainable choice available. However, it’s worth examining the contents more closely.
This ink type not only contains water, but also many binders, pigments and, often, solvents or volatile organic compounds (VOCs) to help it dry quicker or stay open and usable in the screen. As the ink is cured in the dryer, the VOCs are released into the air. A quick glance at safety data sheets may reveal Propylene Glycol (PG), which can be used as antifreeze, or Diethylene Glycol (DEG), another VOC that has been classified as poisonous if swallowed, according to the U.S. National Library of Medicine.
Due to the ink’s water content, mold can grow in the container, rendering it unusable within a year or so. Many manufacturers include additives to inhibit mold growth, while others may aid in better curing or printing. These chemicals may or may not be released into the air during the curing process.
Once plastisol or acrysol ink has been deposited in the screen but not consumed, it can be returned to its original container. Since these inks contain little to no VOCs, they still are the same as when the container was first opened.
A typical water-based ink would change viscosity during the screen-printing process, as some evaporation occurs. It may be possible to simply add some water to make it a usable product, but it typically requires an additive. Often, the ink is too dry to be properly reconstituted for printing and must be disposed.
Ink Disposal
Regardless of whether you’re using plastisol or water-based inks, both contain chemicals whose disposal is strictly regulated. In all cases, familiarize yourself with local, state and federal rules regarding this process.
Plastisol inks are 100% solids. When fully cured, the PVC resin fully absorbs the ink’s plasticizers to form a plastic ink film or solid. Some municipalities may allow fully cured plastisol inks to be disposed or recycled as regular plastic waste. Uncured plastisol may be eligible for recycling. If not, it likely must be processed by an authorized chemical-waste disposer.
Despite its name, never pour water-based ink down a sink or into the ground, and never throw it in the garbage. Some of its components are considered hazardous. Local laws may allow you to reduce disposal volumes by opening the lids and allowing the water and any solvents to evaporate. The remaining pigmented binder should then be disposed in accordance with local regulations.
Printing Parameters
The importance of using the correct emulsion mainly applies when using water-based ink, as plastisol and acrysol inks use the standard emulsion types. Water-based inks require a specific emulsion that is more durable and can withstand contact with water.
For larger projects, a hardener is added to ensure the stencil doesn’t break down, but this can make reclaiming the emulsion from the screens difficult — even impossible. Also, the screen mesh would need to be torn out and restretched. The additional hardener and mesh replacements will add to the screen’s overall cost.
Inks behave differently in cold or hot weather. On colder days, plastisol ink may be thicker than on hotter days — which can be corrected by adding heat in your shop — but little else affects its workability. This also is the case with acrysols. Simply printing the ink a few strokes will make it creamy again. Some users preheat the ink to room temperature, but keeping it off the floor and above 50°F usually will suffice.
Water-based inks perform best when the humidity is higher than when it is lower. Some screen-printing equipment manufacturers even offer humidifiers with their machines to help keep sensitive ink flowing. Take this into consideration when deciding on an ink system to purchase.
In colder climates, you may need to add a heating unit to allow the ink to properly flow on the screens. Humidifiers can corrode machines over time, but remember that both solutions add costs to your bottom line. Also, some of the driest locations also are the coldest, which can make water-based inks dry in the screen more quickly.
Some inks also require pallets to be preheated to a certain temperature before printing can begin, thus requiring additional downtime before production and consuming precious energy resources.
TIP:
Pallet Adhesive
A water-based pallet adhesive is more efficient than a spray adhesive. Although the latter may be convenient, much of the adhesive and its chemicals get dispersed in the air during application.
Part 2 of this series will cover substrates, ink costs, flashing, curing and test printing.