Sustainability in the Screen Printing World? It’s Complicated
September 02, 2020
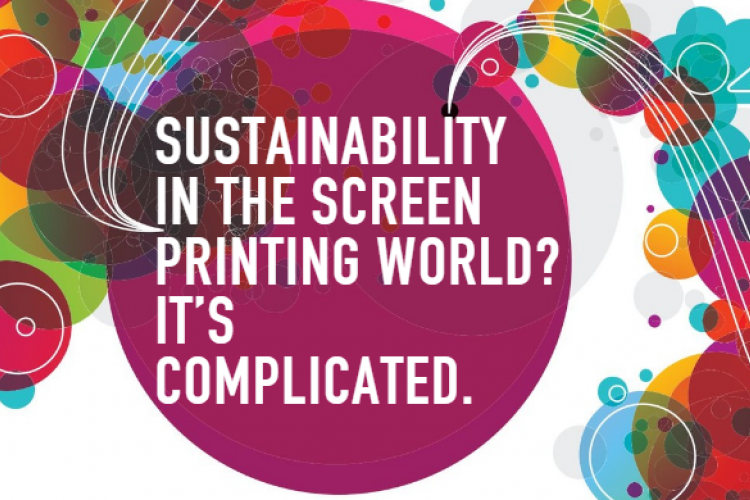
Global apparel is a trillion dollar industry that keeps us all clothed, but in the process casts a large footprint on our environment. The average person today buys 60% more clothing than they did 20 years ago and they throw out more as a result. Less than 1% of used clothing today is recycled or reused. According to the World Bank, the fashion industry uses over 93 billion cubic meters of water. That’s enough to meet the needs of five hundred million people. An estimated 20% of wastewater worldwide comes from fabric treatments. The fashion industry contributes 10% of annual global carbon emissions, more than all international flights and maritime shipping combined. At its current rate, the fashion industry’s greenhouse gas emissions are expected to increase by more than 50% in the next 10 years.
These statistics are sobering and have brought needed attention and urgency to how the industry can become more sustainable and environment-friendly. There is much opportunity for gain, particularly given the apparel industry’s size and the scale of its impact.
There has been a lot of good and science-based progress made in recent years. But at the same time, we have seen an increase in bold and unsubstantiated claims suggesting that various apparel-related products are ‘greener’ or ‘eco-friendlier’ than others. Since these claims are largely unregulated, it should come as no surprise that many are unsupported by the facts, and are misleading or flat out wrong. For example, organic cotton shirts to some may seem like the ‘greener’ choice over polyester. But would it change your perception if you considered that it takes hundreds of gallons of water to grow, dye and treat one shirt, and that many polyester shirts are now being spun from recycled plastic products?
This article takes a closer look at the environmental impact of screen printing inks - the primary consumables for apparel decoration. As a supplier to the industry, we are often asked why certain screen print ink products (such as water base inks) are represented as environment-friendly and others (most notably, PVC plastisols) aren’t. Is one truly friendlier to the environment or more sustainable than the other? Not necessarily. Certainly there are differences between PVC, acrysol and water base ink products, but they are all plastics. Yes, water base inks, like plastisols and acrysols, are plastics.
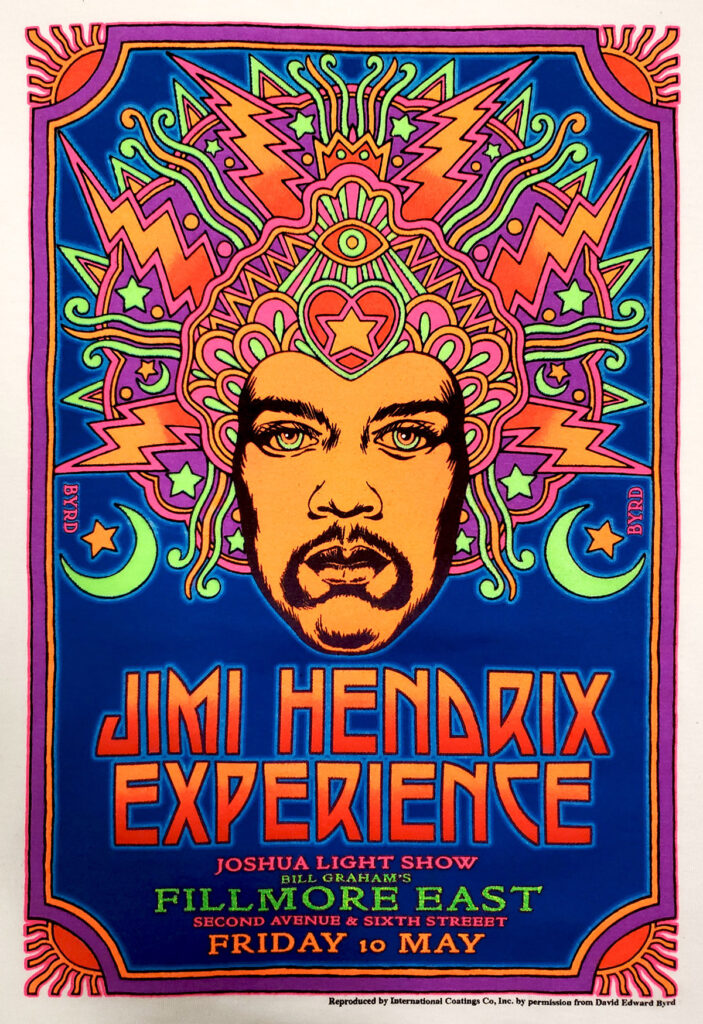
Fact or Fiction?
PVC plastisols have been and continue to be the inks of choice in North America for good reason. They are versatile, easy to use, cost efficient and safe. Plastisols don’t dry in the screen because they don’t cure until they are heated. Plastisols are considered ‘100% solids’ and consequently provide virtually a 100% yield. What you print on the garment stays on the garment. Most water base inks contain 20 to 30% solids. The highest solids water base inks contain no more than 70% solids.
Printers looking for an alternative to PVC are generally looking to acrysol or water base inks. Like plastisols, acrysols are 100% solids and provide the same high yield. They are easy to use, and print and behave like PVC plastisols. They don’t dry in the screen and most don’t require a flash after every print.
There is a misguided notion that water base inks consist of water and pigments. That is incorrect. All water base inks contain a plastic binder (usually an acrylic or urethane) and various additives (pigments, fillers, retarders) that are suspended in water and other co-solvents. In fact, many high-solids water base inks contain relatively little water. Water base inks aren’t as popular as plastisols in North America largely because they’re not as easy to use (drying in the screen), not as efficient (lower yields, daily cleaning, more waste), require more energy and time to cure, and in the case of some ‘high-solids’ inks, are more expensive.
Claims that water base inks are more environment friendly than plastisols and acrysols are questionable at best. All three inks rely on plastic resins or binders, pigments, fillers and various chemical additives. Plastisols and acrysols contain plasticizers that cross-link with the plastic resin. These plasticizers don’t evaporate off but become part of the ink film. Water base inks, on the other hand, rely on solvents that evaporate off leaving the pigmented binder compounds on the garments. These evaporative solvents may represent over 70% of the ink. While the primary solvent is water, water base inks often contain co-solvents such as alcohols, glycols and formaldehyde. These co-solvents may be harmful and put printers at risk unless they are properly protected from the evaporative fumes.
Footprint
Plastisols, acrysols and water base inks have environmental footprints that are quite different. Water base printing generally requires more energy to power more flashes and cure/ventilate (to drive off the moisture), and more water (primarily for daily cleaning). At the end of a print day, plastisol and acrysol can be left on the screen or put back in the bucket for use at another time. Not necessarily so with water base inks. Water base printing consumes more water and generates more water waste, and that waste quite often is poured mistakenly down the drain.
The common misconception is that water base inks are benign since they are largely water. Not so. They are chemical compounds that, aside from their harmful co-solvents, contain other chemicals (binders, fillers, additives, mold inhibitors and pigments). Some of these chemicals are considered hazardous and must be managed as such. Plastisol and acrysol waste that can’t be reused can often be recycled for other uses or when cured can be disposed as a regular plastic. Water base binder in some cases may be disposed similarly if all solvents have evaporated off.
The point here - take the time to learn which inks work best for your situation. I’m not suggesting that plastisols and acrysols are better than water base inks. But at the same time, water base inks aren’t necessarily better or greener than plastisol or acrysol inks. Remember that in the end how you manage your shop – materials, energy, workflow, reuse/recycle and waste - will largely determine how ‘green’ your operation is.
So the next time you hear a claim about one product being green or greener than the next, take the time to understand the basis of that assertion. It just might be that someone is trying to ‘greenwash’ their products.
Steve Kahane is International Coatings’ President and CEO. Prior to joining International Coatings, he held senior executive positions in the environment and engineering fields, and served on the faculty of the UCLA School of Public Health where he taught a core course on environmental health.
International Coatings manufactures a complete line of non-phthalate plastisol and acrysol screen printing inks, including a wide variety of whites, specialty inks, special effects inks, color matching systems, additives and reducers. For more information on their products, please visit www.iccink.com