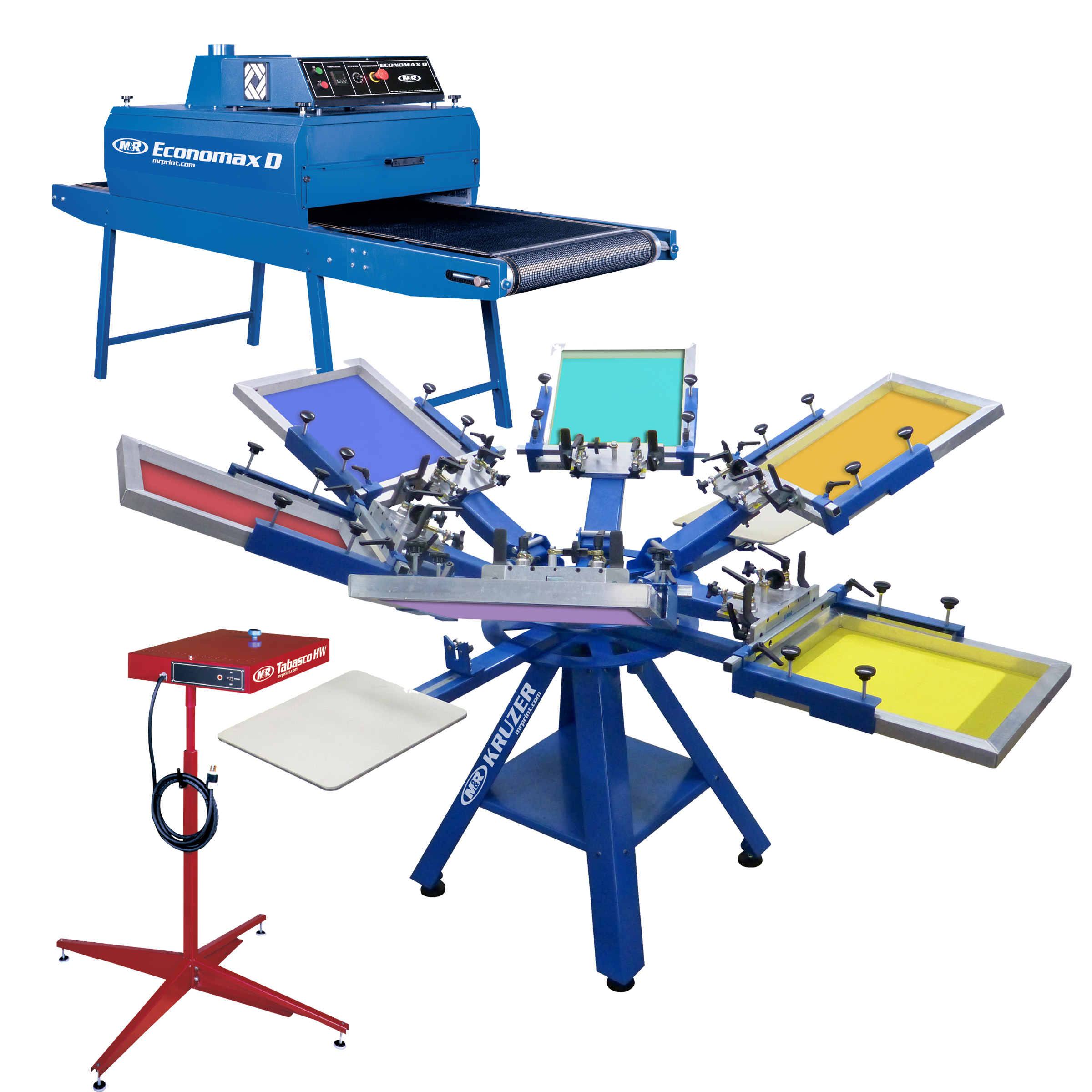
Here is Part II of John Levocz' article, published on
Printwear, on what printers need for a start-up (Read Part I on our blog):
CHOOSE A PRINTER
There are many types and styles of manual printers in the market place, but they're ultimately all designed to complete the same process. Some print better than others, but the job at hand is to enable a printer to print sing;e or multiple-color designs onto garments quickly, efficiently, and in registration.
Look for a printer that's expandable. This could be a printer that expands from a single color to four colors or four colors to six colors. It's less costly to expand this way as opposed to buying new equipment because you outgrew what you originally purchased. Given the designs and types of garments that are printed today, start with a four-color printer with four stations for loading, flashing, and cool downs. Also, consider a printer with micro-registration for a quicker and easier job setup.
Buying a printer is like buying a car. Visit your distributor's showroom if possible and take a test drive. Do the micros move smoothly? Does the press spin freely with minimum effort? Remember, if all goes well, you'll use it all day. As for the references of other decorators who use this equipment. If possible, call them to get their opinion. As long as you're not in direct competition, most are willing to answer a few questions regarding the press they purchased.
FLASH CURE UNIT
Along with the printer, you need a flash-cure unit. This equipment enables you to flash your under base, so you can print on dark garments and specialty pieces. A flash cure unit is an essential piece of equipment in your shop. These units operate at high temperatures to gel the ink before moving to another screen, especially on designs that cannot be printed wet-on-wet.
Considering the high operating temperature, an automatic-style flash is a good option. This type of flash stays over the garment and moves away after a specified time to eliminate burned shirts and, even worse, burned platens on your press that would have to be replaced. In my experience, I can almost guarantee that if you opt to not get an automatic flash, you will get distracted and burn shirts and platens.
DRYERS
After the printing is complete, the garment now needs to be cured or dried. Standard plastisol inks require 325 degrees F at specified times for a proper cure. You can have the best artwork and nicest design, but if the ink washes off the first time your customer cleans the shirt, you won't be in business long. Proper curing is an important part of screen printing and should not be overlooked.
For a startup business, I recommend an electric infrared conveyor drying system. These dryers convert infrared energy to heat to cure the printed garments. As with presses, many dryers are expandable in length, so the dryer can grow with your business. If you saved some money in other areas look for a 36 belt width. This allows for a press on each side of the dryer as your business grows. And with all the different types of material printers are asked to decorate these days, good airflow is a must. This airflow helps eliminate scorching and shrinkage and solidly cures the decorated garment.
John Levocz, International Coatings’ Northeast regional sales director, has been in the screen printing industry for more than 30 years and has broad experience in graphics and textile printing. John is a contributor to International Coatings’ blogs and holds print seminars all over the country.
International Coatings manufactures a complete line of Centris™ non-Phthalate screen printing inks, including a wide variety of whites, specialty inks, special effects inks,color matching systems, additives and reducers. In addition, International Coatings also manufactures a line of AXEON™ non-Phthalate, non-PVC special effects inks. For more information on our products, please visit our website at www.iccink.com.