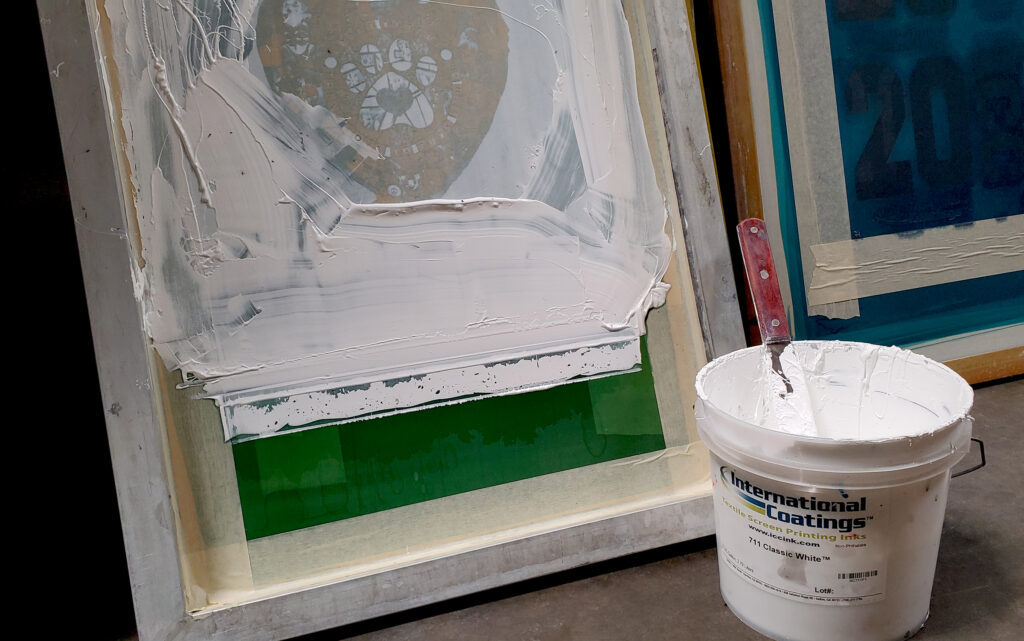
Whether you use water-base, plastisol, or acrysol inks, there are best practices on how to safely and responsibly dispose of screen print waste.
Check out Kieth Stevens’
Impressions Magazine article below on how to properly dispose of ink and other screen printing waste:
Every so often I am asked how to dispose of unusable inks. The answer is not as simple - or as complicated - as it seems. With sustainability and environmental protection at the forefront, knowing how to properly dispose of ink – and other screen printing waste - is crucial.
Unfortunately, this topic is not often discussed at symposiums or seminars. I cringe to think that uninformed screen printers could dispose of waste in ways that hurt our fragile environment. I am not an expert on the subject, but I have had to deal with this issue throughout my screen printing career.
Screen printing is a process that involves the use of various chemicals. From prepping to cleaning and reclaiming, there are different chemicals involved. First off, read the SDS (Safety Data Sheets) for the chemical products and learn how to properly use them. Check for any potential hazardous ingredients or possible chemical interactions, and how to safely handle the products. Become familiar with the products you are using and how to properly use them.
Next, contact your city or state waste disposal office to determine the waste disposal regulations that apply to you. There are strict regulations for disposing potentially hazardous materials and improper disposal can lead to criminal penalties. It may be a daunting prospect to check with the city or state, but it may help avoid fines and or legal costs in the long run. Let’s explore disposal of the most common types of screen printing inks used today.
Solid Waste
Plastisol is essentially 100 percent solids and can often be disposed as a plastic solid. Simply spread
residual ink on a piece of cardboard and run it through the dryer a few times until it is completely cured. Then it may be able to be disposed of as regular plastic waste. Larger amounts can either be recycled for other uses or cured to form a solid. Once cured, it may also be able to be disposed of as regular plastic.
This method can also be used for most water-base inks, but running the ink through the dryer may not be necessary. Simply letting the ink air-dry or the liquid evaporate should be enough. Some high-solids water base inks
do need to be cured in the dryer as they do not air-dry.
Once again, please confirm with your local regulatory authority on what is deemed acceptable practice before you dispose of plastic solids as regular waste.
This is as simple as it gets. But… what about the stuff left over from your screen cleaning or reclaiming process? This is where things get muddy, no pun intended.
Residual Waste
The next step in the screen print cleaning process is to remove ink from the screen and the various tools used, such as squeegees, spatula, stirring stick, etc. Typically in this step, the ink is cleaned off using solvents or other cleaning liquids. The sludge that is created from the mixture of inks and chemical solvents should
never be flushed down the drain! Instead, it should be collected in a separate tank (container) and when full, disposed of properly. There are many commercial companies (such as Safety Kleen) that can dispose of this waste, as long as the inks and chemicals you use do not contain any of restricted chemicals such as heavy metals (lead, cadmium). They may require a sample of the sludge to be analyzed for assurances.
The approved sludge that the waste companies take away can then be incinerated. Some of the waste may be used as a fuel to heat and create asphalt or in the manufacture of cement. Some of the left-over ash can be blended into the asphalt.
Waste Water
When washing off ink residue with water during the cleaning or reclaiming process, there are certain protocols I feel are mandatory. In particular, it is important to take steps to prevent the inadvertent disposal of residues and wastes down a drain. This protocol should be implemented regardless of whether water-base or plastisol inks are used and should cover emulsion, cleaning, reclaiming, adhesive
s and other chemical waste.
Many shops use commercial industry waste disposal services along with in-house clarifying or chemical recirculating systems to responsibly deal with waste water. Clarifiers are settling tanks, used to remove solid particulates or suspended solids from liquids. Some larger clarifying tanks may have a pre-filtering unit, which will filter out large particles before the water goes into the tank. The clarifier allows the particles of pigment, emulsion or any other solids washed down the drain, time to settle to the bottom. If your shop does not use much water, the clarifier could be as small as 10 gallons. Larger shops may need 1 or even 2 tanks holding thousands of gallons each to give the suspended particles time to drop to the bottom. The sludge that collects at the bottom will later be removed for disposal by your waste disposal service. The remaining clear water on top can be re-used or passed down the line to your cities’ water treatment facility.
A chemical recirculating system works like a mini clarifier, except that it re-uses chemicals instead of water. Typically this system can be set up as a wash/cleaning station where the screens and tools are washed with a chemical wash. The waste liquid is collected beneath the wash station and clarified. The clear chemical on top is then syphoned off and reused. A chemical recirculating system can reduce chemical use and save costs.
The amount of residue a shop generates can vary, depending on how well inks are removed from the screens and tools prior to washing. Keep in mind that
anything going down the drain must be dealt with at some point. The better you are at pre-cleaning inks off the screens the better for the environment. Overall, the screen printing industry can really minimize its impact on the environment by diligently disposing of waste in a proper manner.