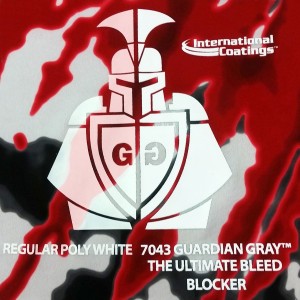
In an article that was recently featured in Screen Printing Magazine’s October/November 2016 issue, and on
Screenweb.com, Kieth Stevens gives us some tips on printing on today's modern fabrics.
Popular, profitable, and often a pain in the neck to print, the latest fashion fabrics can present quite a challenge to shops accustomed to printing standard plastisols on all-cotton garments.
For the most part, today’s ready-for-use plastisol inks haven’t changed all that much over the years, other than the introduction of non-phthalate formulations. (There are, of course, newer non-PVC inks such as silicone, high-solids water based, and acrylic-based plastisol inks, though in this article I’ll be focusing on non-phthalate plastisols.) What has changed, though, are the types and styles of fabrics that printers are asked to decorate.
Over the last several years, the increased cost and lack of availability of cotton has, in part, pressured manufacturers to develop newer fabrics that can be – and often are – challenging to work with. One popular example is the lightweight performance wear that is great for exercising, constructed from a blend of several fibers that each adds its own benefit to the garment. For example, the fabric may be made up of Lycra, which adds stretch; cotton, which adds body; and polyester, which adds lightness and cost benefits.
Battling Dye Migration
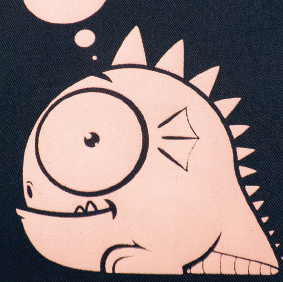
Inks formulated for 50/50 blends or 100-percent polyester fabric typically contain low-bleed ingredients to help reduce dye migration. Also known as bleeding or sublimation, dye migration is sometimes encountered with certain colors of polyester garments. It happens with polyester dyes that were heat-set (meaning cured or bonded) to the fibers at lower temperatures than what the shirts will be exposed to in curing standard plastisol inks. So, when you print these colored polyester fabrics and send them through a conveyor dryer at about 320 degrees Fahrenheit, the dyes are re-released (sublimated) and can turn a white ink design on a red garment into an unwanted pink. I’ve also seen instances where a dark blue or black fabric turned pink, not lighter shades of the base garment color as you would expect. (
Left.) This phenomenon happens when a shirt that was first colored with a red dye is later over-dyed by the supplier with a darker color, possibly to reduce inventory.
Some inks designed specifically for performance fabrics can be cured at lower temperatures (280 to 300 degrees

Fahrenheit) to further combat dye migration. International Coatings'
Performance Pro™ 7100 Series, for example, was formulated specifically for the next generation of performance and athletic fabrics. However, some sublimated fabrics are prone to excessive bleeding even at the lower temperatures, leaving little that can be done to stop the white from turning into an unwanted color. This excessive dye migration is especially common with dye-sublimated polyester garments, often found in camouflage style prints. Bleed-blocking inks are now available that work not just by blocking the sublimating dye, but by actually absorbing it. (
Right.) Typically, these blockers (such as IC's
Guardian Gray 7043) can also be cured at lower temperatures to help further contain the dye.
Stay tuned for Part II..."Giving up the Ghost" and "Stretching for the Cure"
Kieth Stevens is the Western regional sales manager for International Coatings. He has been teaching screen printing for more than 10 years and is a regular contributor to International Coatings’ blogs.
International Coatings manufactures a complete line of Centris™ non-Phthalate screen printing ink
s, including a wide variety of whites, specialty inks, special effects inks,color matching systems, additives and reducers. In addition, International Coatings also manufactures a line of AXEON™ non-Phthalate,
non-PVC special effects inks. For more information on our products, please visit our website at
www.iccink.com.