Printing Basics: Reflective Inks
October 14, 2014
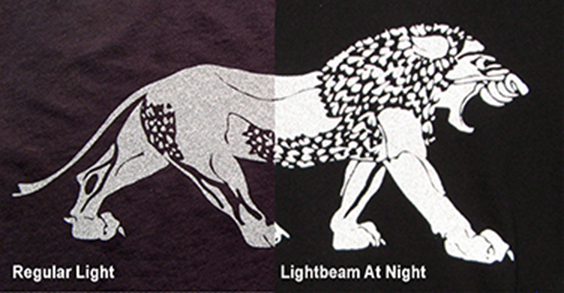
We get calls every week about the proper way to print with reflective inks. Following is a brief explanation by John Levocz, International Coatings' North East Regional Sales Manager, recently published in Impressions, detailing the methods, and reasons behind them, when it comes to reflective-ink printing.
First, always thoroughly stir the reflective ink before printing. Basically, reflective inks are made up of a carrier base and small reflective glass beads. Since the base is thin, the beads will settle if not stirred before printing.
The reflectivity in the ink comes from the reflective beads or particles, not the base. During the course of printing, one flood coat and one squeegee print usually will yield the most reflectivity. By doing this, the base coat will soak into the material, leaving the reflective particles on top of the material so they can reflect the most light. If you do multiple print strokes, you will lay down too much of the base and the reflective beads won’t be able to sit on top of the fabric evenly and properly reflect the light.
Printing reflective ink is not the same as printing white ink on a black shirt, during which the more white ink you lay down, the brighter or more opaque the print is. When printing with reflective ink, less is basically more. Remember to follow all manufacturers’ recommendations for mesh counts, as particle sizes are different and will require different meshes. Using too fine of a mesh count will strain the reflective particles from the carrier base, laying down less than the optimum amount of reflective beads for the best reflectivity. This also will cause the mesh to become clogged with very expensive reflective beads.
For printing on dark colors and when extra opacity is needed, you can print a white underbase and then print the reflective ink on top of it. Just remember that when you do this, you will lose some of the reflectivity due to the base not soaking completely into the material.
Some reflective inks require the use of a catalyst, coupler or adhesion promoter. Basically, they all accomplish the same goal: making sure the reflective beads stay put on the garment. As usual, follow all the manufacturers’ recommendations. They are there for a reason.
When printing reflective inks correctly, they can add a new style of printing to your arsenal. These types of inks can be used as a visibility enhancement on garments for children, as well as for athletic gear like running shirts. With Halloween right around the corner, printing shirts with reflective inks could be a good choice.
John Levocz is North East regional sales manager for International Coatings. For more information, visit iccink.com and read the company’s blog.
International Coatings' Oplilux® Reflective ink systems are one of the brightest reflective inks in the market. Optilux® consists of our 505 Reflective and 507 Enhanced Reflective inks. Click here for more info.
International Coatings manufactures a complete line of phthalate-compliant screen printing inks, including a wide variety of whites, specialty inks, special effects inks, color matching systems, additives and reducers. For more information on our products, please visit our website at www.iccink.com.