Pointers for Prepress Success - Part I
February 07, 2019
In a recent article in Impressions Magazine, Kieth Stevens was asked what steps should be taken during the prepress process to ensure a successful print process.
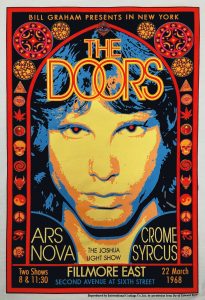
Use these tips for proper prep prior to screen-printing production:
There are several details to consider when preparing to screen print a garment. The following are six that I consider of utmost importance for achieving a great print.
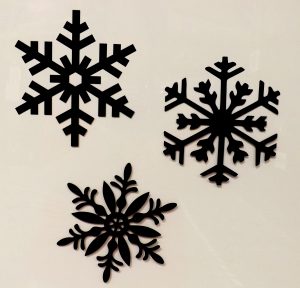
1. Dense Film:
One of the most important pre-press items to prepare is dense film. When you hold the film up to a strong light, does it show through the dark, positive areas? In a perfect world, no light should penetrate. While it's possible to get decent results with a small amount of light showing through, it's not the best scenario.
Many shops use pure photopolymer emulsion. But if your film is not super opaque, you may have to underexpose your image because the emulsion is so sensitive that it sees a small amount of light showing through where it shouldn't. In order to get a decent image, cut back the amount of light so that the resulting image is satisfactory given the circumstances.
However, by underexposing the screen to compensate, the emulsion does not get enough of the needed light and can fall apart during the production run. You also may find that tiny pinholes can be seen from the dust and dirt particles that probably would have been exposed away if the screen received enough light.
2. Correct Mesh Selection:
Always take a moment to look at an imaged film and select the best screen mesh needed for the job. The ideal mesh count would not be so high that it requires a double pass or so low that the print would lose fine details.
I've had the privilege of visiting many large shops to help them improve quality and make more money. They all have one thing in common: "hungry" machines, or screen-printing presses that can "chew through" 3,000-4,000 or more shirts per day. Keeping these machines "fed" and running smoothly is critical.
Imagine having to do 80,000 prints every 24 hours; it can't be achieved if you don't select the best mesh for a particular design. Choosing too fine of a mesh will result in having to either re-burn the screen to a more open mesh, select a softer-squeegee or double-stroke the print. Regardless, it'll cost time and money, so selecting the correct mesh the first time is critical.
3. Tight Mesh:
While the correct mesh count is important, equally important is tight mesh tension. Tight screen mesh can be an accurate gauge of a shop's print quality.
The mesh opening is the key. Mesh selection is instrumental in determining the mesh opening, but tighter mesh has a larger opening. Imagine a rubber band; the further you stretch it, the thinner it gets. The same thing happens when you properly stretch screen-mesh fibers; they get thinner and open the screen mesh to allow ink to flow easier.
Imagine trying to cut cheese with a thick, old and loose wire; it would be much harder than if you were using a fine wire that is tight. Now, imagine trying to cut a slice of cheese every 4 seconds with a loose wire. This also would be very difficult, but it would be much easier with a tight wire. Tight screen mesh functions the same way.
Large shops know this and make it standard practice to maintain their mesh tension. Doing so can make a job profitable in varying degrees. We're talking about the difference between a car payment or a house payment - and maybe even a second house payment if you've been doing this correctly for a certain amount of time.
Also, the tighter the mesh, the less pressure required for the squeegee to transfer ink onto the substance. Additionally, the amount of off contact needed with a properly stretched screen is far less and the overall quality will show.
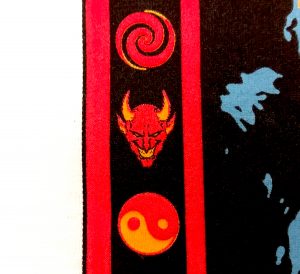