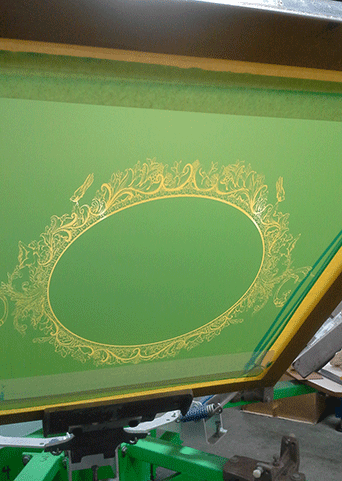
Is it important to really know the cost-per-screen for your business? This was a question posed by a
Printwear reader, and here is Kieth's response:
It is important to know the cost-per-screen in your shop since the health and profit of your business depends on it. Costs generally stay the same but can vary depending on what type of ink you use. For example, some special effects inks may be more expensive than regular inks and if you print inks that require a heavier emulsion deposit (high density for example), the extra cost for the emulsion also needs to be factored in.
In general, ink costs-per-shirt are relatively low, approximately five cents-per-shirt. To calculate costs-per-screen, factor in the cost of the emulsion (total cost of emulsion divided by the number of screens a bucket will coat), which typically averages to about one dollar per screen. Then calculate other screen-making costs such as tape, film, and the cost of time and labor to prepare a screen.
One sure way to keep costs under control is to make the screens right the first time. This is one of the most important things to control. Fixing issues like pinholes or ghosting costs time and money and create delays in production.
The cost of materials for production is very important, but keep in mind that the old saying still is true: “You get what you pay for.” What’s the point of saving a few dollars on a gallon of ink or emulsion if it slows down your production in some way? I’ve been at high-volume plants where they used cheaper ink, yet they had to stop the production every hundred prints or so to clean off the screen due to build-up. It’s what you ship out that you get paid for and if you ship less, then you get paid less. Saving a dollar can cost you hundreds, if not thousands, in the long run.
Kieth Stevens is the Western regional sales manager for International Coatings. He has been teaching screen printing for more than 10 years and is a regular contributor to International Coatings’ blogs.
International Coatings manufactures a complete line of Centris™ non-Phthalate screen printing inks, including a wide variety of whites, specialty inks, special effects inks,color matching systems, additives and reducers. In addition, International Coatings also manufactures a line of AXEON™ non-Phthalate, non-PVC special effects inks. For more information on our products, please visit our website at www.iccink.com.