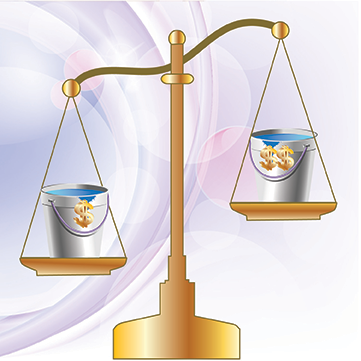
With budgets getting tighter and tighter, everyone wants to save money. So how much money can you really save with cheaper inks? Here is Kieth Stevens with food for thought relating to cheaper inks, an article recently published in
Impressions:
What does it take to achieve the maximum amount of prints per day, per hour or per minute at the lowest overall price?
After all, the more prints you get out the door at a faster rate, the more money you can make. Sounds logical, right?
What then, is the best strategy for attaining that maximization goal? There are many variables to consider, but let’s focus on inks. Often, printers think that purchasing the cheapest inks will achieve the maximum profits needed at a lesser cost. It could, on some rare occasion, but most likely it won’t. While all cheap inks aren’t bad, you must compare apples to apples and test the inks.
Cheap inks often use cheaper ingredients, which may not result in high-performance ink. Some of my customers only purchase high-end inks because they know they can rely on ink performance and, thus, save money overall.
How so? For example, if you could print 12 prints per minute with the ink you are using, but you find that a cheaper ink slows you down to 11 prints per minute because of a slower flash speed, the cheaper ink can cost you dearly.
Let’s say you are charging $0.50 per impression (or whatever you are making per print) at a rate of 720 impressions per hour (12 prints per minute at $0.50 per print). That gives you $360 per hour. In our example then, the newer, less-expensive ink slowed your press down to 660 shirts per hour, which gives you a gross loss of $30 per hour.
What about ink yield? If the ink you are using costs $50 per gallon and, because it is of good quality, you can get a decent print through a 160 mesh and you found that you are getting a yield of 800 prints per gallon, then the ink costs per print is $0.0625.
Let’s assume that the less-expensive ink costs $45 per gallon but upon printing, you find it is a little less opaque, so you may need a softer squeegee or lower mesh to get the same opacity as the original ink. This will result in a lesser yield to, say, 700 prints per gallon, which gives you a per-print cost of $0.0642. Combine this with the loss due to the slower flash and the “cost saving” will cost you dearly in both time and money.
So be careful, and do your homework. In these cases, you get what you pay for.
Kieth Stevens is the Western regional sales manager for International Coatings. He has been teaching screen printing for more than 10 years and is a regular contributor to International Coatings' blogs.
International Coatings manufactures a complete line of phthalate-compliant
screen printing inks, including a wide variety of
whites,
specialty inks,
special effects inks,
color matching systems,
additives and reducers. For more information on our products, please visit our website at
www.iccink.com.