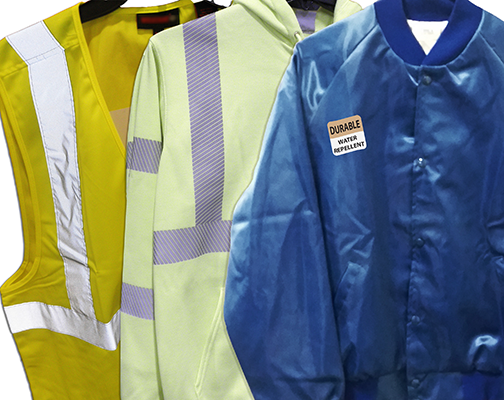
The term "
workwear" covers a large range of imprinted clothing. Everything from industrial uniforms to safety and specialty clothing all fall under this category. However, although these diverse end uses are technically the same, the requirements of each industry can vary drastically. In this article, recently published in
Printwear Magazine, John Levocz breaks down each major industry and looks at common differences to help you be successful in printing these garments.
Industrial style uniforms
Industrial style uniforms can be any type of cotton, 50/50, or polyester uniforms worn by workers that have some type of print on them. Uniforms that require industrial laundering such as mechanics’ uniforms, restaurant wear, or any others that are worn in a very dirty environment will not be a candidate for standard plastisol inks. Instead, most of these uniforms use some sort of emblem—either embroidered, heat transferred, or screen printed—to embellish the uniform.
If the garment is screen printed, it is done so with a solvent-type ink system able to withstand aggressive industrial wash cycles and high temperatures. Plastisol ink can only withstand normal home wash temperatures and cycles. Other industrial style uniforms that do not require industrial laundering can use standard plastisol inks. Low bleed plastisol for 50/50, and inks designed for polyester are the latest craze for garments used in the workforce. Generally, these uniforms are worn in warehouse environments where industrial laundering is not required. Even though these uniforms can use plastisol ink, a full and proper cure is essential to keep a lasting print.
Beware that some of these uniforms are made of heavyweight materials that can soak up the heat in your dryer and prevent the ink from reaching the proper cure temperature. Try to run similar materials together to reduce cure issues. Since the heavier fabric may require a longer dwell time and higher temperatures, running a heavyweight work shirt and a lightweight white T-shirt down the same oven chamber at the same time can lead to under-cure or scorching.
Remember, the ink on a work shirt should be visible. Always use the mesh count recommended by the ink manufacturer to get the proper ink lay-down and appearance that the customer wants and expects. On uniforms and work shirts, you are looking for a visible and long lasting print, not a soft feel with low visibility. Pay attention to emulsion coating, mesh count, and cure temperature to create a highly visible and long-lasting print.
Outdoor clothing
Outdoor workwear usually consists of different jacket styles or sweatshirts. Most sweats worn as workwear are usually 50/50 or 100 percent polyester. The 100 percent polyester helps repel moisture and is usually more comfortable and lighter to wear during a full workday. For 50/50 sweats, a good low-bleed ink printed through the proper mesh count and with just enough pressure to lay the ink on top of the garment should do the job and exhibit a visible, long-lasting print. As always, the proper emulsion coating and cure temperature will go a long way in creating a durable print.
The 100 percent polyester garment can present some unique challenges. When printing on 100 percent polyester garments, the biggest issue will be bleed; aka dye migration. Bleed occurs when the polyester dyes release from the fibers and travel through the ink film. This causes the ink film to show the color of the dyes. The bleed issue is usually very pronounced on maroon and red colored garments, but it can happen with any colored garment, although the darker the garment color and the lighter the ink color, the more noticeable it is.
What makes polyester bleed is the heat required to cure standard plastisol inks. Heat causes the dye to release from the polyester fibers and migrate through the ink film to appear on the top layer of ink. A good low-bleed ink can often stop this dye migration before it reaches the top of the ink surface and turns the ink to the garment color. Remember, the ink needs to migrate completely through the ink film for it to turn colors. This can take 24-plus hours to completely occur, so a test print the day before starting production on the garment with the ink you will be using is recommended. This is not always easy but more cost effective than having to replace the shirts and printing them all over again.
Other types of outdoor workwear include work jackets. Most jackets are either nylon, polyester, or some form of cotton or canvas. Polyester jackets require the same steps and precautions as polyester sweats do to minimize bleeding. Nylon jackets use basically three different types of weaves: taffeta, oxford, and satin. The taffeta weave is a plain weave where the yarns alternately pass over and under each other. The oxford weave is a basket weave of two threads over and two threads under. The satin weave is a weave that produces a very lustrous fabric and is used to make satin jackets.
When printing on nylon jackets, an ink specifically designed for nylon is always the best choice. These inks are a two-part system that uses an adhesion promoter or catalyst to provide the necessary adhesion and abrasion resistance needed for outdoor jackets. As always, follow all the manufacturers’ recommendations on mesh counts and the amount of catalyst or adhesion promoter to be added. Weigh the components to avoid any failures after printing.
Some jackets have a water-repellent coating that will potentially become an issue when printed on. The coating is designed to help water from saturating the garment, but depending on how heavily it blocks water, the coating can also inhibit ink from bonding correctly to the jacket. If the ink is not bonding correctly, the abrasion resistance and adhesion will be compromised.
To check for a water-repellent finish, pour a small cup of water on the garment. If it beads up and does not soak in after a few minutes, you could have an adhesion issue. Wiping the print area with isopropyl alcohol can help remove some of the coating and allow you to get better adhesion.
Safety workwear
In today’s safety minded workforce, high-visibility clothing is highly sought after. Standard high-visibility yellow and orange work shirts are mostly cotton or polyester. You’ll note that most workwear in the marketplace—and other garments for that matter—are made of polyester.
Most of these shirts or sweats can be printed in the same way as cotton, however, you do need to account for bleed on polyester. The big issue with safety garments is when reflective ink needs to be added. Most of the straight-line reflective areas on these garments consist of reflective tape applied during the manufacturing process. These tapes meet the safety specifications for reflectivity set up by the government. However, more and more printers are getting requests from customers—especially EMTs, police or firefighters—for a reflective print, such as a logo or other marking. While these designs can be printed using a reflective screen printing ink, the designs will not meet the government specifications for reflectivity like the tapes do.
All reflective inks work in a similar fashion. A reflective bead is mixed into a base, and when printed, the base will soak into the garment and leave the bead partially exposed to light, reflecting light back to the source. Depending on how much bead is exposed and the orientation of the bead, the reflectivity can change. For this reason, it won’t pass reflectivity tests set up by the government. This is also why screen printed reflective ink is considered a visibility enhancement.
Most reflective inks are either water-based or plastisol-based products. Many use a coupler to ensure that the bead is locked into the ink film when fully cured and will not release from the garment during normal wash cycles. When printing reflective ink, remember that less is more. One flood stroke and one print stroke using the mesh counts recommended by the manufacturer will give you the brightest and most durable print.
Band aids
When printing workwear, I like to keep the following products on hand for challenging situations:
- Stretch additive: This will allow the ink greater stretch.
- Low-cure additive: This will allow the ink to cure at a slightly lower temperature to help reduce bleed and help with any shrinkage issues.
- Low Bleed Reducer: If your inks need to be reduced, error on a low-bleed reducer to help with bleed.
Now that you know which inks to use with which fabrics, printing on workwear is hopefully less daunting. While the term workwear might be new to you as a screen printer, it can definitely be a growing part of your business. By following ink manufacturers’ recommendations and doing the proper testing, it can be a profitable addition to your company.
John Levocz is the North East regional sales manager for International Coatings. For more information, visit iccink.com and read the company’s blog
International Coatings manufactures a complete line of non-phthalate
screen printing inks, including a wide variety of
whites,
specialty inks,
special effects inks,
color matching systems,
additives and reducers. For more information on our products, please visit our website at
www.iccink.com.