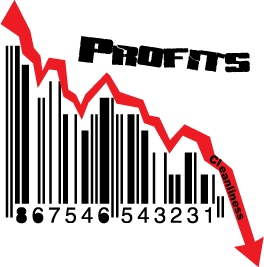
Is there really a link between cleanliness in a print shop and profits? How “clean” does the workspace have to be? We asked our Western Regional Sales Manager, Kieth Stevens, to give some insight on this issue:
“Well here I go trying to come up with a way to start the conversation on the importance of cleanliness in a shop.
I have worked in a lot of shops and have visited 100s and one thing that I have noticed is that it’s not an accident to see a correlation between a well-run successful shop and a haphazardly-run one that is not as successful.
But why is organization and cleanliness linked so closely to the bottom line and profitability?
I have visited shops that haven’t cleaned their floor space under and around a press in years. The ink and adhesive build-up on the floor has gotten so thick, one could actually trip over it. At other shops I have seen equipment covered with lint so deeply that the original color of the equipment can’t even be discerned.
I encountered some shops where I’ve seen food remnants strewn all over the place; so much so that the filth attracted rodents who then gnawed on the wiring of the equipment, thus rendering the equipment unusable and in need of serious repair.
I have been to shops located off of dirt roads whose managers don’t understand why they have to constantly clean the glass on their exposing machine (due to dust from the dirt roads). For one thing, the images on the resulting screens will be compromised and with that, the quality of the prints.
Another observation which makes me cringe is when I see liquids exuding from squeegees which then tint and contaminate the inks in the screens. Such contamination could have easily been prevented by simply cleaning off the left-over cleaning liquids off the squeegees correctly.
In another instance, I was visiting a shop that was printing quarter million piece runs, using a white ink for an underbase. The white-ink screen is located right next to the person loading the shirts. Before loading the pallet, every shirt gets a shake-off to remove excess lint or possible left-over sewing threads. So bear with me: After the shake-off, the lint and sewing threads are now momentarily air born and some will either wind up in the screen and some will wind up in the open pail of white ink next to the white printing head. After tens of thousands of prints, the white screen has now been “filtering” the lint and sewing threads from the ink that has passed through the screen that which now has accumulated in the white screen. This accumulation will affect the quality of the prints and the ink now needs to be removed and disposed of.
If management does not have a process in place to dispose of such contamination correctly, the contaminated ink may end up back in the bucket and then will end up as a problem when the ink is used on the next job.
All of these senarios depict print shops that are loosing profitability. A clean and organized shop usually means that the management values quality. Ultimately, if the print shop can deliver consistently high quality and value to the customers, the shop will benefit.
My examples above – all true – seem exaggerated, but I can assure you that a lot of unnecessary expenses and loss of production time result from lack of cleanliness. Not only is quality being affected, but safety as well.
Need another reason for keeping things clean and organized in your shop? With today’s push towards “green and compliant” products, contaminated garments may cost you more than you bargained for in terms of fees and/or penalties. I’ll write more about this in another blog soon.”
For more information on International Coatings ink products, please visit our website at
www.iccink.com.