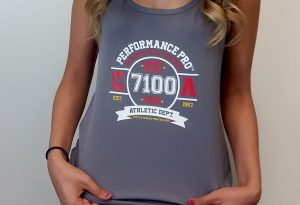
In a recent article published by Impressions Magazine, Kieth Stevens gives us some tips on printing athletic numbering.
The major change in screen printing numbers has been the number of fabrics on the market. Here's how to tackle the challenges these options can create:
After 43 years of screen printing, I have helped, seen and advised many customers regarding screen-printing best practices for achieving the best results for numbering. The difference, if any, between printing numbers 20 years ago and now is the plethora of fabric options available on the market today. Not surprisingly, many tips for this kind of printing also can be applied to everyday garment printing to improve results.
To start, I am a huge proponent of quality screens. Mesh selection and tightness are important, as is starting with a dense film positive — which will be addressed shortly. Emulsion thickness also is important. To create good numbers, use a thicker emulsion over mesh (EOM). This is achieved when the amount of emulsion is much thicker than that of the mesh. This requires dense film to ensure proper emulsion exposure.
Choosing the Right Ink
Selecting the proper ink to be used for athletic numbering can be daunting. Should you use nylon or polyester ink, or maybe just general ink type? Should you use a catalyst or dye blocker? There is a dizzying array of options, so the following is a breakdown of them all.
Polyester. The correct ink choice for numbering will be determined mainly by the fabric type or garment being printed. If it’s a red or dark- colored, 100% polyester fabric, then you should use a low-bleed polyester white ink as an underbase. If the garment is made of polyester fabric that has been dyed red — or any other dark color or pattern — via sublimation, then consider using a dye-blocking underbase that is gray or black (
Guardian Gray or
Guardian Black), and then can be over-printed using a polyester white ink.
Whether a garment was sublimated often can be determined by looking at its inside. If it’s white and the outside is a different color, then it has been dyed via sublimation. Always make an effort to ascertain the fabric type you are printing — it’s better to be safe than sorry.
Nylon. If you’ll be printing a nylon garment, there typically will be no dye migration or bleeding. Use inks that specifically are formulated for nylon (
All-Pro™ 900 Series), as their properties make them more durable. However, consider whether to use a
catalyst to promote better ink adhesion to the slippery fabric.
For example, if the nylon or another synthetic fabric is smooth and shiny, the ink may have difficulty sticking to the garment — hence the need for a catalyst. But if the fabric has some openness to it — or “fur” — then the ink should adhere without the catalyst.
Some fabrics also may have a chemical treatment or coating that can make it difficult for the ink to adhere. The added chemical could have properties that make the fabric water-repellent, such as a rain coat or umbrella. Printing on these pretreated fabrics can be challenging. It may even be worth it to attempt to remove the coating or treatment in the area in which you want to print. Removal can be done by dabbing some Isopropyl alcohol on the area to remove or dilute the coating to help the ink adhere.
Athletic fabrics. What about stretch? Many new fabrics types, especially athletic styles that often are numbered, contain multiple yarn varieties, including combinations of rayon, polyester, nylon, cotton and Lycra. Use an ink with built-in, enhanced stretch or use a stretch additive to give the ink film more elongation (
Performance Pro™ 7100 Series).
Performance fabrics. Many new fabric types, especially those containing synthetics, appear “normal” but can be more sensitive to heat. Fortunately, many ink manufacturers now offer a variety of low-cure inks that typically cure at 275°F (
FlexCure™ Line). If you want to turn an ink you already have on the shelf into a low-cure type, simply mix in a
low-cure additive that will reduce the cure or fuse temperature into the 275°F range. However, using low-cure inks alone doesn’t completely preclude the problems that can be caused by printing these heat-sensitive fabrics.
Heat is a necessary evil in our industry. It’s needed to cure or fuse the ink, but it can become an enemy after the ink has reached the required cure temperature. For example, if the fabric is a dark sublimated polyester, then the dye may bleed if it gets too hot. So keeping the garment as cool as possible after the ink has reached the cure temperature is a must.
Avoid stacking hot garments; use a cooling fan at the end of the dryer or shake hot garments to cool them before stacking them in two or more piles.
A flash unit also is a heat source, so remember to only flash the ink to a “dry-to-the touch” state and nothing more. Over-flashing can cause intercoat-adhesion problems, which occur when a color is printed on top of another that has been over-flashed. The top color doesn’t bond with the over-flashed ink, causing them to peel apart.
Garment usage. To make it a bit more complicated when discussing the right ink choices when printing athletic numbers, also consider how the garment will be used. Printing a volleyball jersey that won’t undergo a lot of contact, meaning the printed ink film won’t be susceptible to much abuse, is different than numbering a high school football jersey. With the latter, a lot of contact (rubbing, scratching etc.) can be expected, so the ink needs to be more durable.
In such situations, choose an ink that produces a tough surface — such as one formulated for nylon — not one containing blowing agents, i.e., puff or suede, as those ink types are not as resistant to scuffs and scratches. A high-quality ink may cost a little more because of the quality of the ingredients, but will be worth it in the long run.
More Printing Tips
Many athletic garments are misprinted due to insufficient off-contact. The screen should peel away from the garment as soon as the squeegee has deposited the ink. Also, keep your screen mesh as tight as possible and group screens. Translation: When printing numbers, use screens with the same type of tension to avoid blurring.
When decorating athletic uniforms, multiple images usually are involved, including a team logo, the player’s name and the number. Not only have you invested in the garment itself, but printing one or more impressions means you have wasted time and labor. It’s important to ensure everything is in order to achieve a correct print.
Also, remember to use the correct pallet adhesive. A water-based adhesive will leave little to no residue inside the garment. Spray adhesives, on the other hand, can leave residue inside the garment when the pallets get hot during the printing process.
Having opaque film means your exposures are easier and more forgiving. Thick emulsion will help not only in the ink film’s opacity, but also by separating the screen mesh from the garment, resulting in a smoother image. Lower mesh counts are used to get good coverage when printing athletic images, but there also is more potential for the image edges to appear rough. Thicker emulsion reduces the rough edges and the denser, more opaque film allows better emulsion exposure. A film positive that is more transparent likely will under-expose the screen to get the image to develop.
The same basic principles that apply to general screen printing also apply to athletic numbering. To support the increase in synthetic fabrics being used for athletic and performance garments, lower-curing, bleed-blocking and stretchy inks have been developed to achieve great prints on these new options.
Visit our
FlexCure™ page flexible curing inks that work great on heat-sensitive fabrics.