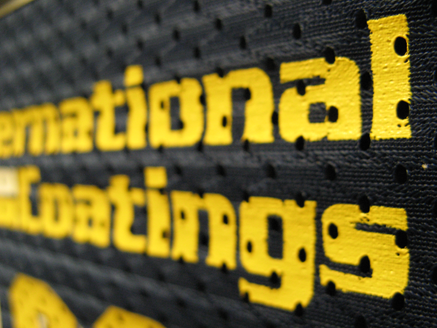
Here is an excerpt from an article on performance wear, written by Ed Branigan and recently published in
Impressions Magazine. To read the full article,
click here:
Printing onto sportswear used to be a straightforward affair. Whether it was for a basketball or football team order, the fabric used was (for the most part) made of 100% polyester or a blend — usually with something stretchable such as Lycra spandex. The printing itself could be difficult — especially on athletic mesh material — but with patience and practice, great results were achievable. Polyester dye migration was the biggest issue printers usually encountered.
In recent years, we have seen the development of a broad range of new synthetic fabrics in the sports and athletic market. The terms “anti-wicking” and “dry fit” are entering the screen printing vernacular. The content of these different fabrics vary, but all have fallen under the umbrella term of “performancewear.” Polyester still is the dominant material element, but now the stretchable portion has risen from 5%-10% to 15%-20%.
There also are newer materials, such as Tactel nylon, or those with properties like the popular retail brand Under Armour — many of which are not only harder to screen print on, but also are heat-sensitive fabrics. Many fabric types and materials are being imported from all over the world and they all are different. Dye migration still is the largest problem to deal with, but some of the newer garments exhibiting heat sensitivity and extra stretch have become compounding problems.
DEFEATING DYE MIGRATION By far, the most difficult — and often most baffling — problem affecting many screen printers is polyester dye migration. How many times have printers thought they did everything correctly, yet the white ink on a red polyester shirt still turned pink? The critical issue as far as dye migration goes is heat, and this is a very important point to remember.
Polyester dyes are synthetic, so they don’t absorb dyes like a natural fiber, such as cotton, would. They need help to do this. The polyester dye pigment molecules are sublimated at temperatures in the 260°F-270°F range, then chemically sealed onto the fiber.
Plastisol inks, on the other hand, need higher temperatures to cure — typically in the 300°F-320°F range. Put properly, the ink needs to become fused instead of cured. The two main components of plastisol are resin and plasticizer. When mixed, they stay wet for a long time. Once heat is applied, the resin begins to absorb the plasticizer. For textile plastisol inks, once the 300°F-320°F range is attained, the two elements become fully fused, or 100% solid.
When printing on polyester, the problem begins once the garment is exposed to temperatures beyond the 260°F-270°F range, which causes the dye to be set. At this stage of the ink-fusing process, there is the danger that the polyester dye will be sublimated again. If this happens, the plasticizer in the ink will try to “pull” the polyester dye molecules up into itself. This can happen either immediately, days or even weeks later. Once the dye molecules have become gaseous, the proverbial genie is out of the bottle.
There are two main ways to combat dye migration....
Read more
International Coatings recently released a new product specifically designed for printing on difficult performance and athletic garments: the
7100 Performance Pro Series.
International Coatings manufactures a complete line of phthalate-compliant
screen printing inks, including a wide variety of
whites,
specialty inks,
special effects inks,
color matching systems,
additives and reducers. For more information on our products, please visit our website at
www.iccink.com.
International Coatings: The Intelligent Choice